Summary Statement
A general treatment of fall fatalities and fall protection with a focus on the Ontario (Canada) construction industry.
1999
Get the edge on falls
Despite variations in fatality causes and frequency, falls remain the number one killer in Ontario construction.
- Construction workers have fallen off edges of every description. The most common are floors, roofs, and openings in floors and roofs. When an unprotected edge makes you worry about falling, take action. Set up guardrails, install opening covers, or use a fall-arrest system securely tied off.
- A number of fatal falls have occurred among small crews doing jobs of low cost and short duration. Contractors evidently thought the jobs were small and quick enough not to warrant fall protection. That was their fatal mistake.
- Construction workers have been killed when they removed the plywood cover from a roof or floor opening to use the material elsewhere and inadvertently stepped into the opening. Covers should be clearly identified in bright paint: OPENING COVER! DO NOT REMOVE!
- Your chances of falling from a ladder are significantly reduced if you maintain three-point contact when climbing up and down the ladder or working from it. Three-point contact means one hand and two feet or two hands and one foot on the ladder at all times.
- Construction workers have been killed when they fell from ladders that slid or slipped because the ladders weren't secured at top and bottom. In addition, use a mudsill to support ladder feet on soft, uncompacted, or rough soil.
- On scaffolds and other work platforms where personnel can fall 2.4 meters (8 feet) or more, guardrails must be installed or a fall-arrest system must be worn.
- Construction workers have been killed by falls as low as two feet. Where practical, install guardrails even on low work platforms. When working from any raised surface, remember where you are. Don't step backward. Don't shift footing without looking down first.
In Ontario
construction, falls have accounted for at least 30 deaths
since 1995.
1995
1996
1997
1998
Fall
Fatalities
6
8
8
4
Total
Fatalities
13
23
15
24
In 1999,
seven of the 12 construction fatalities so far have been from
falls.
Ministry
of Labour (MOL) inspectors have stepped up enforcement of
fall protection requirements. The most important initiative
is the move towards province-wide mandatory fall protection
training, expected to be included in revised regulations.
Prevention
starts with guardrails
|
|||||||||||||||
|
|||||||||||||||
|
Guardrails are the first line of defense in fall prevention. They should be installed along the open sides of any area where a worker may fall 2.4 meters (8 feet) or more or into water, operating machinery, or hazardous substances. Areas to be protected include
- floors and floor openings
- balconies
- slab formwork
- stairways and landings
- roof tops
- scaffolds and other work platforms
- runways and ramps
- bridge surfaces.
Guardrails should have a top rail, mid-rail, and toeboard secured to vertical posts or supports.
Available in wood, wood-slat, wire rope, and manufactured wire mesh systems, guardrails must meet the following minimum dimensions:
- top rail between 91 cm (3 feet) and 1.07 meters (3 feet, 6 inches) high
- toeboard at least 10.2 cm (4 inches) high and installed flush with the surface
- posts no more than 2.4 meters (8 feet) apart.
These components should be secured to the inside of the posts or jacks. Toeboards should be installed on all open sides of a scaffold or work platform.
Guardrails should be installed as close to the edge as possible and must be capable of resisting any load likely to be applied. This may require extra reinforcement in special situations, such as where forklifts or buggies are used.
For maximum resistance to sideways force, the 2x4 top rail of wooden guardrails should be laid flat, with the larger dimension horizontal. To further strengthen guardrails, double the top rail and reduce the spacing of posts to between 1 and 2 meters (3 feet 4 inches and 6 feet 8 inches.)

Wood guardrails must be supported by posts extending to the top rail and braced and solidly fastened to the floor. Shoring jacks used as posts should be fitted with plywood softener plates at top and bottom. Snug up and check the posts regularly for tightness.
For slabs and the end of flying slab forms, manufactured posts can be attached to the concrete with either clamps or insert anchors.
If guardrails must be removed, the opening edge should be roped off and marked with warning signs. In addition, workers should use a fall-arrest system properly anchored and tied off.
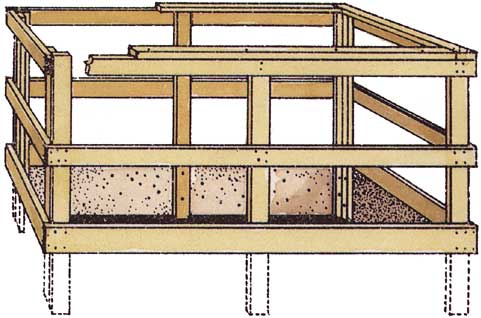
In construction, eliminating the risk of falls may not be possible. It then becomes essential to select proper fall protection.
Two basic types of fall protection are
- fall arrest
- travel restraint.
Where guardrails or other protection is not in place, you must use a fall-arrest or travel-restraint system if you are in danger of falling
- more than 3 meters
- into operating machinery
- into water or another liquid
- into or onto a hazardous substance or object.
Fall Arrest Fall arrest is the most common system. It stops a fall within a few feet of the worker's original position. A full body harness is required with a fall-arrest system. A typical system consists of the following parts connected together:
A fall-arrest system must be worn when you are on a rolling scaffold that is being moved or when you are getting on, working from, or getting off suspended access equipment such as a swingstage or bosun's chair. |
![]() |
Travel-restraint systems prevent falls by restraining a worker from getting too close to an unprotected edge.
A travel restraint system must be arranged to keep the worker back from the fall hazard area. The system usually consists of
- safety belt of full body harness (CSA-certified)
- lanyard
- rope grab
- lifeline
- lifeline anchor.
The basic problem with travel-restraint systems is that the rope grab must be continually adjusted to allow free movement and travel but still keep the worker away from the edge. One technique is to use a self-retracting lifeline (see article below).
In practice, travel-restraint systems are not foolproof because the length of the lifeline is not always adjusted properly. If the self-retracting lifeline, for instance, is longer than the distance to the nearest edge, a worker moving in that direction will not be restrained before falling.
But even if the system doesn't prevent a fall, it still arrests the fall.
Self-retracting lifelinesSelf-retracting lifelines (SRLs) are widely used in construction to provide fall protection, especially where workers must move about to handle or install material. SRLs let the user move the full length of the line but stop and lock at any sudden pull. This action is designed for fall arrest -- not for travel restraint.
Users of SRLs most know the manufacturers' recommendations for proper operation as well as any safeguards required for specific applications.
SRLs have traditionally been anchored above the worker's head with the line running near vertical down to the worker's safety belt or harness. There's general agreement that this is the best application of SRLs.
In construction, however, different applications have appeared. In addition to the traditional position, two other basic options are
- anchor and unit at the ridge of a pitched roof above the worker's location
- anchor and unit situated on a flat work surface so that the lifeline is drawn out by the worker in a horizontal plane.
![]() |
Each manufacturer's manual provides information and guidelines for SRLs anchored above a worker's head. Not all of the manuals, however, cover the use of SRLs in horizontal applications. In these cases the user must confirm that the particular model is approved for horizontal use. The manufacturer will then outline requirements for proper horizontal use. Remember -- SRLs are NOT travel restraints. Travel restraints are designed to restrain the user's movement near open edges and prevent falling altogether. The only time an SRL can act as a travel restraint is when the line is completely drawn out yet still short enough to keep the user from moving forward or laterally into a hazardous location. |
Fall-arrest systems can only prevent fatal falls if they are used properly. Correct use includes inspection. Your life depends on it.
Harness- Always check the tag for date of manufacture. Most web-type harnesses have a service life of five years. If the harness doesn't have a tag, don't use it.
- Look for cuts, fraying, broken stitching, and other damage to webbing. Check for chemical or heat damage.
- Inspect metal buckles for distortion, cracks, and sharp or rough edges. All buckles should slide easily for adjustment.
- Check for worn, cut, or frayed fibers where buckles attach to harness.
- Inspect D-ring for distortion, cracks, sharp or rough edges, and chemical or heat damage.
- Ensure that the plate holding the D-ring in position is free from cracks, heat damage, and other defects. The plate must keep the D-ring from sliding out of place.
Most lanyards have a service life of five years. Check tag for date of manufacture. Inspect lanyard for worn, broken, or cut fibers; signs of stretching; evidence of chemical or heat damage; and cracked or distorted connecting hardware.
Shock AbsorberA shock absorber should carry a tag indicating date of last inspection. If the tag is missing, return the absorber to your supervisor for advice on its suitability. If the absorber is made with tear-away stitching designed to absorb fall-arrest load, make sure stitching is intact.
![]() |
Snaphook
|
Rope
Grab
- Make
sure that grabs are installed rightside up. Most grabs feature
a directional arrow to indicate proper orientation.
- Ensure
that proper size lifeline is used. The required size is marked
on the rope grab.
- Mount
the grab on the lifeline. Pull the grab down sharply. The
grab should lock within 30 cm (12 inches).
Rope Grab
|
![]() |
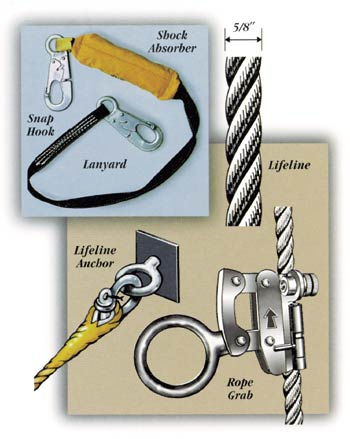
Lifeline
Lifelines
must be at least 16mm diameter polypropylene or material of
equal strength. Inspect lines from end to end before installation.
Look for cuts, burns, fraying, and chemical or heat damage.
Signs of decreased diameter may indicate that line has been
involved in a fall arrest and should be discarded.
Lifeline
Anchorage
- Ensure
that lifelines are securely attached to solid anchor points.
- Whenever
possible, attach only one lifeline to each anchor.
- Never
anchor to bundles of material that may be moved or depleted
through use. Do not anchor to exposed rebar unless embedment
length is adequate.
![]() |
Lifeline Lifelines must be at least 16mm diameter polypropylene or material of equal strength. Inspect lines from end to end before installation. Look for cuts, burns, fraying, and chemical or heat damage. Signs of decreased diameter may indicate that line has been involved in a fall arrest and should be discarded. Lifeline Anchorage
|