Building Safer Highway Work Zones: Measures to Prevent Worker Injuries From Vehicles and Equipment
Summary Statement
A comprehensive study of fatalities and injuries in highway workzones and a set of measures that can be taken to reduce them.
April 20001
Case Examples of Highway Construction Fatalities
Since 1982, NIOSH has conducted site investigations of workplace fatalities through the Fatality Assessment and Control Evaluation (FACE) program, a research program for the identification and investigation of fatal occupational injuries. The goal of the FACE program is to collect information on factors that may have contributed to occupational fatalities, using an epidemiological approach, and to develop and disseminate recommendations for prevention of similar incidents in the future. The FACE program has conducted investigations of machinery-related fatalities since 1994, and in the fall of 1999, began to target highway work zone fatalities. FACE investigations are conducted by staff from the NIOSH Division of Safety Research, and by FACE programs housed in state departments of health or departments of labor, with technical assistance provided by NIOSH.The product of each FACE investigation is a narrative report describing the incident and providing recommendations for prevention. FACE investigators draw upon multiple sources to gather information needed to develop a report: employer and witness interviews; coroner, medical examiner, police, or OSHA reports; death certificates; equipment operator's manuals; and manufacturers' representatives. The role of FACE is not to place blame for the fatality or to assess compliance with safety and health regulations. Rather, as a research program, it seeks to provide concrete, practical recommendations that can be applied to prevent similar types of fatalities.
The following case examples underscore the fatality risks faced by those who work near vehicles and machinery in work zones and in ancillary areas that serve as staging, or support areas for the work zone (e.g., temporary batch plants). Although most of the examples involve highway construction, a few cases that occurred in maintenance and utility work zones are also included. Each case example consists of a summary of the incident and the prevention recommendations put forth by the investigator. The full text of the narrative reports on which these case examples are based may be found at http://www.cdc.gov/niosh/face/faceweb.html. It is hoped that these examples will be of use to construction contractors, contracting agencies, and safety professionals in assessing hazards in their own workplaces and communicating those hazards to workers.
Sources for Case Examples
Case #1. Minnesota Department of Health [1992]. Highway paving crew member dies after being run over by a rear end dump truck. Minneapolis, MN: Fatality Assessment and Control Evaluation (FACE) Report No. MN9207.
Case #2. Minnesota Department of Health [1992]. Highway construction flagman dies after being struck by a pickup truck. Minneapolis, MN: Fatality Assessment and Control Evaluation (FACE) Report No. MN9214.
Case #3. Minnesota Department of Health [1993]. Worker dies after being run over by a dump truck. Minneapolis, MN: Fatality Assessment and Control Evaluation (FACE) Report No. MN9219.
Case #4. Minnesota Department of Health [1993]. Road paving crew member dies after being run over by a digger derrick truck. Minneapolis, MN: Fatality Assessment and Control Evaluation (FACE) Report No. MN9300801.
Case #5. New Jersey Department of Health [1994]. Road construction laborer dies after falling underneath the wheel of a front end loader. Trenton, NJ: Fatality Assessment and Control Evaluation (FACE) Report No. 93-NJ-090-01.
Case #6. Maryland Division of Labor & Industry [1994]. Construction foreman crushed by excavator-Maryland. Baltimore, MD: Fatality Assessment and Control Evaluation (FACE) Report No. 94MD063.
Case #7. Minnesota Department of Health [1995]. Highway construction worker dies after being struck while crossing roadway. Minneapolis, MN: Fatality Assessment and Control Evaluation (FACE) Report No. 94MN03101.
Case #8. Nebraska Department of Labor [1995]. Asphalt roller crushes flagman. Omaha, NE: Fatality Assessment and Control Evaluation (FACE) Report No. 94NE059.
Case #9. NIOSH [1994]. Tree trimmer foreman dies after being struck by a pickup truck—South Carolina. Morgantown, WV: U.S. Department of Health and Human Services, Centers for Disease Control and Prevention, National Institute for Occupational Safety and Health, Division of Safety Research. Fatality Assessment and Control Evaluation (FACE) Report No. 94-07.
Case #10. NIOSH [1994]. Asphalt milling superintendent crushed under asphalt milling machine—Virginia. Morgantown, WV: U.S. Department of Health and Human Services, Centers for Disease Control and Prevention, National Institute for Occupational Safety and Health, Division of Safety Research. Fatality Assessment and Control Evaluation (FACE) Report No. 94-18.
Case #11. Minnesota Department of Health [1997]. Conveyor operator dies after being run over by belly dump trailer. Minneapolis, MN: Fatality Assessment and Control Evaluation (FACE) Report No. MN 96-92.
Case #12. NIOSH [1994]. Laborer dies after being struck by overturning crane—Virginia. Morgantown, WV: U.S. Department of Health and Human Services, Centers for Disease Control and Prevention, National Institute for Occupational Safety and Health, Division of Safety Research. Fatality Assessment and Control Evaluation (FACE) Report No. 94-19.
Case #13. Massachusetts Department of Public Health [1996]. Construction laborer crushed by asphalt truck while paving interstate highway. Boston, MA: Fatality Assessment and Control Evaluation (FACE) Report No. 95-MA-039-01.
Case #14. California Department of Health Services [1996]. Crane operator falls 30 feet while working from a freeway overpass in California. Los Angeles, CA: Fatality Assessment and Control Evaluation (FACE) Report No. 95CA01101.
Case #15. NIOSH [1998]. Construction laborer dies after being run over by asphalt roller at highway construction site—Virginia. Morgantown, WV: U.S. Department of Health and Human Services, Centers for Disease Control and Prevention, National Institute for Occupational Safety and Health, Division of Safety Research. Fatality Assessment and Control Evaluation (FACE) Report No. 98-06.
Case #16. Minnesota Department of Health [1995]. Construction worker dies after 9-wheel pneumatic roller rolls over on her. Minneapolis, MN: Fatality Assessment and Control Evaluation (FACE) Report No. 95MN04701.
Case #17. Missouri Department of Health [1995]. County highway department worker crushed when dump truck and trailer tipped over. Springfield, MO: Fatality Assessment and Control Evaluation (FACE) Report No. 95MO057.
Case #18. University of Iowa [1996]. Asphalt machine runs over and kills worker-Iowa. Iowa City, IA: Fatality Assessment and Control Evaluation (FACE) Report No. 96IA55.
Case #19. Missouri Department of Health [1996]. Highway department supervisor struck by reversing dump truck. Springfield, MO: Fatality Assessment and Control Evaluation (FACE) Report No. 96MO012.
Case #20. NIOSH [1996]. Equipment operator dies after scraper overturns—Virginia. Morgantown, WV: U.S. Department of Health and Human Services, Centers for Disease Control and Prevention, National Institute for Occupational Safety and Health, Division of Safety Research. Fatality Assessment and Control Evaluation (FACE) Report No. 96-16.
Case #21. Missouri Department of Health [1997]. Asphalt roller operator dies following rollover incident. Springfield, MO: Fatality Assessment and Control Evaluation (FACE) Report No. 97MO037.
Case #22. NIOSH [1997]. Construction laborer dies after being struck by a front end loader at a construction site — Pennsylvania. Morgantown, WV: U.S. Department of Health and Human Services, Centers for Disease Control and Prevention, National Institute for Occupational Safety and Health, Division of Safety Research. Fatality Assessment and Control Evaluation (FACE) Report No. 97-11.
Case #23. Minnesota Department of Health [1998]. Worker dies after being run over by a front end loader. Minneapolis, MN: Fatality Assessment and Control Evaluation (FACE) Report No. 98MN030.
Case #24. Minnesota Department of Health [2000]. Laborer run over by dump truck while paving parking lot. Minneapolis, MN: Fatality Assessment and Control Evaluation (FACE) Report No. 99MN03201.
Case #25. Minnesota Department of Health [1999]. Electrician dies after falling from cherry picker basket. Minneapolis, MN: Fatality Assessment and Control Evaluation (FACE) Report No. 99MN01801.
Case #26. Wisconsin Division of Public Health [1999]. Heavy equipment operator pinned after bulldozer slides off flatbed trailer. Madison, WI: Fatality Assessment and Control Evaluation (FACE) Report No. 99WI04101.
Case #27. Nebraska Department of Labor [1999]. Member of road crew struck by semi. Omaha, NE: Fatality Assessment and Control Evaluation (FACE) Report No. 99NE021.
Case #28. NIOSH [2000]. Female construction worker dies in a compactor tip over at a highway construction site—South Carolina. Morgantown, WV: U.S. Department of Health and Human Services, Centers for Disease Control and Prevention, National Institute for Occupational Safety and Health, Division of Safety Research. Fatality Assessment and Control Evaluation (FACE) Report No. 99-03.
Case #29. NIOSH [1998]. Laborer run over by dump truck at roadway resurfacing operation—Virginia. Morgantown, WV: U.S. Department of Health and Human Services, Centers for Disease Control and Prevention, National Institute for Occupational Safety and Health, Division of Safety Research. Fatality Assessment and Control Evaluation (FACE) Report No. 98-19.
Case
#1: Highway Paving Crew Member Dies After Being Run Over by a Rear
End Dump Truck
|
A 45-year-old member
of a highway paving crew died as a result of being run over by a rear end
dump truck that was backing up on a section of highway under construction.
The incident occurred on a blacktop mat which was the underlayment for concrete
paving the crew was laying that day. The victim and two helpers were setting
reinforcing rods on the mat, over which concrete would be spread.
The victim had completed his work and was watching the paving operation.
He was asked to instruct the drivers of a line of seven or eight batch trucks
waiting to drive towards the paver to back up approximately 1000 feet. The
paver had advanced to a position where using the blacktop area in the median
as a turnaround was not possible, and this maneuver was necessary in order
to use another section of the highway.
The victim walked to the rear truck (Truck 1) and gave the driver instructions
to back up. At the same time, another truck (Truck 2) was coming forward
towards the rear of the truck line. As the victim was signaling Truck 2
to stop, he positioned himself in the path of Truck 1 which was backing
up, in that driver's blind spot. Truck 1's driver was backing and turning
into the opposite lane, the lane used to drive away from the paver, to make
right-of-way for Truck 2. Despite Truck 1's having an operational back-up
alarm and attempts by Truck 2's driver to warn him of the danger, the victim
was hit by the right rear dual wheels of Truck 1 and pushed approximately
14 feet on the blacktop. He stated to rescue personnel before transport
that he "thought (he) could make it." He died later in surgery from loss
of blood.
To prevent similar fatalities, investigators recommended the following measures:
- Workers should
direct only traffic moving in one direction at busy, noisy construction
sites.
- Include in employee
safety training information about human inaccuracy in estimating the
arrival time of a moving vehicle.
- Equip trucks used on construction sites with rearview sonar which alarms drivers of close proximity to objects behind them.
Case
#2: Highway Construction Flagman Dies After Being Struck by a Pickup
Truck
|
An 18-year-old highway construction flagger died as a result of traumatic injuries received after he was struck by a pickup truck. A highway crew was milling the surface of a bridge approach in preparation for resurfacing. This job was being performed at night during minimum traffic hours; the incident occurred at approximately 3:00 a.m. The milling machine had advanced from the north towards the bridge approach and the job was near completion. The posted speed limit for the stretch of highway involved was 55 mph.
The flagger was positioned just at the north end of the bridge, approximately 75 feet in front of the milling machine. He stood just west of the center line in the southbound lane with the milling machine at his back, facing oncoming (northbound) traffic. He was responsible for stopping and directing this northbound traffic. A portable generator with 7-foot-tall floodlights was positioned 15 to 20 feet from the flagger, and the bridge was well lit by street lights. Traffic signs, cones, and beacon lights were appropriately in place throughout the construction zone. The victim was outfitted with a full reflective vest, reflective pants, and hard hat. It was a clear night and visibility was good.
A pickup truck traveling north at approximately 55 to 60 mph approached the bridge. It advanced across the bridge in the wrong (southbound) lane, directly towards the flagger, who was standing in that lane. The truck struck the flagger, then moved into the correct (northbound) lane before striking the milling machine and other workers, and carried the victim approximately 200 feet before coming to rest in the road at the north end of the bridge. There was no indication of the truck slowing or stopping before impact. The flagger was pronounced dead at the scene of multiple severe traumatic injuries.
To prevent similar fatalities, investigators recommended the following measures:
- Reduce the posted
traffic speed limit through highway construction and work zones.
- Post law enforcement vehicles and/or personnel near and before highway construction zones to capture drivers' attention and ensure that traffic slows before entering the work area.
Case
#3: Road Paving Crew Member Dies After Being Run Over by a Dump
Truck
|
A 27-year-old member
of a road paving crew (victim) died of injuries he received as a result
of being run over by a dump truck. The fatality occurred as the crew was
laying blacktop in two lanes of a four-lane residential city roadway. Dump
trucks were being used to haul blacktop to a paver, which was situated on
a north-southbound road. Trucks waiting to dump their load of blacktop were
parked around the corner from the paver. The victim's dump truck was parked
in the inner lane of this road, facing west. Tack, a sticky liquid spray
used between two layers of blacktop for better adhesion, had been sprayed
in the outer lane of the work area. Trucks were able to drive on the tacked
area of the road if necessary, but the surface was too sticky for other
equipment, such as rollers.
While the victim's truck remained idling, he left the cab, apparently to
check something underneath it or to adjust its brakes. A hammer and the
wrench used for brake adjustment were found near him after the incident.
He was positioned between the cab and the rear tandem wheels of the truck
on the passenger side. A roller approaching from the west was unable to
pass the truck because it could not proceed in the tacked lane. The operator
approached the idling truck on the driver's side, entered the cab, and released
the parking brake. He did not see the victim, who was located on the passenger
side of the truck. He put the truck into gear and drove it forward approximately
15 feet to make enough clearance in the inner lane for the roller to pass.
The truck driver was run over and killed in the process.
Another nearby truck driver, observing that the victim had been run over,
immediately dialed 911 from his cellular radio. First responders attempted
to resuscitate the victim, but he died en route to the emergency room of
multiple traumatic injuries.
To prevent similar fatalities, investigators recommended the following measures:
- Use of a lockout-tagout
system should be required when vehicles are left unattended or undergoing
repair/adjustment.
- Wheels of vehicles undergoing repair or adjustment should be chocked to help prevent unintentional movement of the vehicle.
Case
#4: Worker Dies After Being Run Over by a Digger Derrick Truck
|
A 23-year-old apprentice lineman died of injuries he received after being run over by the tandem dual rear tires of a digger derrick truck. The construction company the victim worked for had been subcontracted to frame and set new electrical poles along a 2-mile stretch of paved county road. The digger derrick truck with an attached boom was used for hole digging and pole stabilization during the setting operation. The crew had been on site for 3 days, and several poles had already been framed and set.
The crew had returned to work after the lunch break, forgetting to don their high-visibility vests. At this time, two company vehicles were parked on the shoulder of the road about midway between two poles in the northbound lane. The crew began work by setting and backfilling pole #1 with the digger derrick, then walked south in the northbound lane to pole #2. They were about 30 feet in front of the digger derrick truck, which was proceeding in reverse to the same pole at about 2 miles per hour. Approximately halfway between pole #1 and pole #2, the victim knelt with his back to the truck to apparently inscribe a word or initials into some soft seal coating. The truck driver, not seeing the victim in his blind spot, continued backing. The victim was hit and run over by both sets of tandem dual rear tires on the passenger side of the truck before it could be stopped. The victim was pulled from beneath the truck and CPR was immediately initiated by coworkers. First responders arrived on the scene within 5 minutes, but the victim was pronounced dead at the scene of multiple traumatic injuries.
To prevent similar fatalities, investigators recommended the following measures:
- Consider equipping
vehicles with additional mirrors to help eliminate the blind spot behind
vehicles, or utilize infrared or ultrasonic devices to detect the presence
of objects behind the vehicle.
- Consider equipping
vehicles with audible back-up alarms.
- Consider implementing a safety policy which assigns one person per site the responsibility for directing vehicles, and specifies site locations for other pedestrian personnel.
Case
#5: Road Construction Laborer Dies After Falling Underneath the
Wheel of a Front End Loader
|
A 39-year-old road construction laborer was killed after falling beneath the wheel of a moving front end loader. The incident occurred during a paving operation in a large suburban housing development. The victim was in one of three crews working in different parts of the development under the supervision of a roving foreman. He had been assigned to work with a front-end-loader operator to chip and fill in the asphalt around manhole covers in preparation for paving. At about 12:15 p.m., the crew completed work on a manhole near a T-intersection of two roads. The driver then started moving the front end loader to the next manhole, located about 50 yards away. Hitching a ride, the victim jumped onto the loader's battery box, which was part of a side step leading up to the driver. The site foreman and a neighbor saw the loader move slowly up the road and turn onto the next street. As the loader climbed a slight incline, the driver stated that the victim (who was apparently engaging in horseplay) grabbed at the forward/reverse control lever on the loader. The driver told him to stop, but he again grabbed at the lever and moved it. This caused the machine to go into reverse, jarring the victim off the loader. He fell three feet to the ground, and the front wheel of the loader ran onto his chest. The driver immediately stopped the machine and went for the supervisor. The neighbor called for an ambulance. The police and EMS arrived and transported the victim to the local trauma center where he underwent emergency surgery. He died of his injuries 7 hours after the incident. The medical examiner determined the cause of death to be hemorrhagic shock due to multiple devastating injuries.
To prevent similar fatalities, investigators recommended the following measures:
- Employers should
develop, implement, and enforce a comprehensive safety program with
the assistance of a joint labor/management safety committee.
- Employers should
conduct periodic job safety meetings and refresher training.
- Manufacturers of construction equipment should consider installing an interlock system that prevents heavy equipment from suddenly reversing direction.
Case
#6: Construction Foreman Crushed by Excavator
|
A 47-year-old construction foreman was crushed by the crawler treads of an excavator. The company had been contracted to modify existing sewer lines for new home construction. The excavator was being used to dig a trench across a two-lane road, with traffic to be routed around the work zone under flagger control. The victim had given directions to the operator regarding placement of the excavator. After speaking with the operator, he walked around to the opposite corner of the excavator. With his back to the excavator, he leaned over to move an orange safety cone. The west track of the excavator caught the victim's leg, and he fell to the ground face first into the path of the excavator. A witness ran toward the operator shouting to him to stop the machine and move backward off the victim. Another member of the crew radioed the company to notify 911. Paramedics arrived within minutes of the call. The victim was flown by helicopter to a university trauma center where he died approximately 45 minutes after the incident. The medical examiner attributed death to multiple injuries.
According to the witnesses, the excavator was equipped with an omni-directional alarm that was audible when the incident occurred. The machine was new, having logged fewer than 100 hours of operation. All of the controls were reportedly functional and the windows of the operator's station were free of cracks or other impediments to the operator's vision. The upper structure was equipped with parabolic mirrors on the cab (right) and the frame (left). The position and configuration of the upper structure and the position of the boom may have obstructed the operator's view of the track that struck the victim.
To prevent similar fatalities, investigators recommended the following measures:
- Employers should
ensure that employees are instructed to stand clear of heavy equipment
that is maneuvering in a work zone.
- Employers should
ensure that heavy equipment operators who must maneuver equipment with
limited visibility in the direction of travel utilize an employee to
signal the operator from a safe distance.
- Employers should
ensure that heavy equipment operators make every effort to establish
a clear view in the direction of travel before maneuvering a piece of
equipment.
- Heavy equipment and other vehicles should be, when feasible, equipped with devices for visualizing or sensing the presence of humans or obstacles that are in the path of travel.
Case
#7: Highway Construction Worker Dies After Being Struck
While Crossing Roadway |
A 55-year-old construction worker died of injuries sustained after being struck by a vehicle on an interstate highway near a major metropolitan area. The victim and a coworker were assigned to drill holes for installation of steel pipes beneath the highway, using a boring machine. The machine was located in the ditch on the east side of the northbound lanes. Construction warning signs were set up 2,000 feet ahead of the work area. At the time of the incident, the victim's task was to cross the highway lanes to mark the exit location of the hole currently being drilled, as his coworker monitored the gauges on the boring machine. According to witnesses, the victim was not wearing a high-visibility safety vest.
At about 8:30 a.m., when the victim crossed the highway and was near the middle of the left lane, two vehicles traveling in that lane approached him. The driver of the second vehicle momentarily looked to the right, toward the boring machine. When he looked forward again, the vehicle ahead of him had moved one lane to the right, and he saw the victim standing directly in front of him. The driver of the second vehicle turned his vehicle to the right and applied his brakes. The victim was struck by the skidding vehicle and thrown 40 feet, landing in the ditch along the left shoulder of the highway. Emergency medical personnel arrived at the scene within a few minutes. The victim was transported to a local hospital where he died approximately 2 hours later. Death was attributed to multiple blunt force injuries.
The total skid distance of the vehicle that struck the victim was 193 feet. Based on the length of the skid and the dry conditions of the road surface, the state patrol estimated the minimum speed of the vehicle as 61 miles per hour at the time the driver started braking. According to the state patrol officer's report, several drivers who witnessed the incident said that the victim was not watching the traffic as he began to cross the highway.
To prevent similar fatalities, investigators recommended the following measures:
- Employers should
ensure that employees wear high visibility vests or garments while walking
and working on roadways.
- Roadway construction work should be scheduled during non-peak traffic periods.
Case
#8: Asphalt Roller Crushes Flagman
|
A 20-year-old road construction company flagger was crushed to death when he fell from and was run over by an asphalt roller during a highway resurfacing operation. The victim had been employed by the company for 3 days. The roller operator was driving the roller up an approximate 10-degree incline, with the flagger riding on the roller. He attempted to shift into a higher gear as he was moving forward, but the roller did not shift and became stuck in neutral. The roller then began moving backwards down the incline. The operator was unable to stop the roller with the foot brake; he did not attempt to apply the emergency brake. As the roller was going downhill and gaining speed, the operator saw cars approaching on the road. To avoid a collision, he decided to turn the roller into the ditch. He told the flagger to jump clear of the roller when he drove off the pavement. As the roller left the pavement, it appeared the victim was thrown from it. The roller rolled backward into a culvert at an opposite incline, then forward. At this time, the roller drum rolled over and came to rest on the victim's head. A witness immediately directed the roller operator to reverse the roller off the victim. His injuries were too severe for any first aid to be rendered, and he died at the scene of massive head trauma.
Several risk factors may have contributed to the fatality. The flagger was riding on the roller in violation of written company policy prohibiting nonoperators from riding on equipment. Secondly, the operator attempted to shift gears while the roller was in motion, although a placard on the machine stated that doing so could result in loss of control, leading to serious injury or death. The roller operator said this prohibition was not explained to him during the 10 to 15 minutes of verbal training he had received. Finally, inspection of the roller after the incident revealed an aerosol can of starting fluid in the area of the brake pedal. This can may have been lodged under the brake pedal when the operator depressed the pedal, thus preventing the brakes from engaging. Subsequent tests on the roller showed the foot brake to be operational.
To prevent similar fatalities, investigators recommended the following measures:
- Establish a comprehensive
training program for all personnel operating specialized machinery to
include "hands-on" training and documentation.
- Establish a thorough
vehicle maintenance and inspection program.
- Develop, implement and enforce a comprehensive safety program that includes, but is not limited to, training in all hazard recognition.
Case
#9: Tree Trimmer Foreman Dies After Being Struck by a Pickup Truck
|
A 21-year-old tree trimmer foreman died after being struck by a pickup truck as he fed brush into a wood chipper along a two-way, two-lane state highway. The victim and a coworker (a climber) were cutting brush for a utility company along a power line right-of-way. The wood chipper and truck used by the crew were located approximately 4 feet from the edge of the highway. Orange safety cones were placed in front of the truck, at the truck door, at the rear of the truck, and at the wheels of the chipper. Four cones were also set behind the chipper at 15-foot intervals. A 48-inch-square "Utility Work Ahead" sign was placed on the same side of the highway, behind the chipper. The posted speed limit was 55 mph. The workers were wearing green work uniforms without orange vests. Company policy required them to wear safety vests in the woods during the hunting season and at intersections; at other times vests were worn at the foreman's discretion.
At 4:30 p.m. on the second day of work at the site, the two men were feeding brush into the wood chipper attached to their truck. The victim emerged from the woods with an armload of brush as his coworker entered the woods to gather another load. The victim began to feed the brush into the chipper. The coworker heard a loud crash and turned to see that a small pickup truck had struck the victim, then the chipper. EMS personnel who responded could not detect any vital signs. The victim was pronounced dead at the scene by the county coroner, who listed the cause of death as closed head trauma and multiple fractures. The investigating officer estimated the speed of the pickup truck at the time of impact was 50 to 55 mph. The pickup truck driver, who was critically injured, told hospital personnel he had no memory of the incident.
To prevent similar fatalities, investigators recommended the following measures:
- Employers should
ensure that a flagger or lookout is present while work is being performed
on the sides of roadways normally open to the public.
- Employers should ensure that employees wear high-visibility clothing while performing operations on the sides of roadways normally open to the public.
Case
#10: Asphalt Milling Superintendent Crushed Under Asphalt Milling
Machine
|
A 40-year-old asphalt milling superintendent was crushed when the milling machine he was operating overturned off a transporter trailer. The victim had arrived about 1:30 a.m. to complete a milling job after the regular machine operator had quit and left the site. At about 2:45 a.m., the crew began loading the milling machine for transport from the job site. Because of the length of the milling machine, the rear tracks are normally positioned over the axles of the transporter for transport, while the discharge conveyor is over the cab of the transporter's tractor. Positioning the milling machine in this manner requires that ramps be used to enable the machine to negotiate the transition from the transporter's deck in front of its wheels to the deck over the transporter wheels. To accomplish this, the crew placed two wedge-shaped wooden blocks (12- by 12- by 52-inch) in front of the deck transition. The victim began to tram the machine in reverse onto the transporter with the assistance of his coworkers, one positioned on the ground between the transporter and the edge of the roadway and the other positioned behind and to the culvert side of the trailer. As the victim trammed the machine up onto the transporter, the wooden blocks used to elevate the rear end of the machine over the transporter wheels dislodged, and the machine overturned off the transporter into a roadside culvert. The victim was trapped in the operator's station and crushed as the machine rolled on top of him. EMS responded within 15 minutes, followed by the medical examiner. The victim was pronounced dead at the scene of crush injuries to the chest.
To prevent similar fatalities, investigators recommended the following measures:
- Employers should ensure that equipment used for loading mobile machines on transporters is configured so that precise alignment of the machine is not critical to the safety of the operation.
- Consider providing
control station layouts that use dissimilar-shaped control levers for
differing functions, or which include lockout devices to prevent hazards
from inadvertent activation of controls.
- Consider machine operator visibility when developing machine designs and operational procedures.
Case
#11: Conveyor Operator Dies After Being Run Over by a Belly Dump
Trailer
|
A 33-year-old conveyor operator died of injuries he sustained when a belly dump trailer that was preparing to unload gravel ran over him. The victim was working at a job site where gravel for a highway construction project was being dumped by belly dump truck trailers. The trucks drove up a ramp composed of sand and gravel to an unloading platform, where the gates of the trailers were opened and the loads emptied into a grating system on a conveyor belt. The victim had been assigned to operate the generator of the conveyor system. As the first truck of the day approached, the driver informed the victim he was going to pour alcohol in the lines that operated the gates of the belly dump trailer to prevent the lines from freezing. The driver then pulled onto the ramp and made two unsuccessful attempts to open the gates from inside the truck cab. The victim, seeing that the gates were not opening, ran up the side of the ramp, which was outside the truck driver's field of vision. He went to an area under the trailer, where there was a lever that could be used to manually open the gates. The truck driver, noticing that other trucks were queuing up behind him, began to drive down the ramp to clear the way for other trucks to dump their loads and to make room for a mechanic to repair his trailer. The driver of the truck immediately behind him, who had observed the victim go under the trailer, attempted to contact the truck driver by radio. However, the truck was already in motion, and the victim was run over by the dual rear wheels on the passenger side of the trailer. Emergency personnel were contacted, but the victim was pronounced dead at the scene. The cause of death was transected thoracic aorta as a result of a pedestrian-dump truck accident.
To prevent similar fatalities, investigators recommended the following measures:
- Employers should
ensure that belly dump trailers are equipped with a manual gate- release
lever located on the side of the trailer rather than underneath the
trailer.
- Employers should
ensure that employees only perform tasks which they have been trained
to do.
- Employers should develop and implement a comprehensive safety program.
Case
#12: Laborer Dies After Being Struck by Overturning Crane
|
A 24-year-old construction laborer was fatally injured when a crane being used to lower a bucket of gravel from the shoulder of an interstate highway into a drainage ditch tipped over. The six-person crew began work at 7 a.m. They positioned a 22-ton capacity, rough terrain, hydraulic crane along the highway shoulder to lower buckets of gravel and concrete down to the ditch line, about 20 feet below the shoulder's edge. The crane was set up on fully extended outriggers, with the left side outrigger floats placed on stacked wooden blocks, which provided additional bearing surface on the shoulder's newly placed fill material. The blocks also tipped the crane slightly toward the highway for additional resistance to the load. This procedure had been followed by the crew in response to a tipping incident that had occurred 3 weeks earlier. A 1/2-cubic-yard capacity bucket attached to the crane's load line was used to lower concrete or gravel into the ditch. The victim's task was to trip the bucket's discharge mechanism and pour out the contents.
At about 10:30 a.m., after a break, the crew repositioned the crane along the shoulder to access the unfinished area of the ditch. While part of the crew set forms in the ditch, the victim, one laborer, and the crane operator began depositing and spreading gravel. At approximately 10:45 a.m., the crane operator was lowering a load of gravel (approximately ¼ cubic yard) to the victim when the ditch side outrigger floats slipped off the timbers, allowing the crane to slide and tip over toward the ditch. As the crane tipped, the head sheave of the boom struck the victim, fracturing his skull and amputating his right arm above the elbow. One of the crew immediately called the emergency medical service (EMS), which responded within 10 minutes and pronounced the victim dead at the scene. The medical examiner determined the cause of death to be skull fracture.
To prevent similar fatalities, investigators recommended the following measures:
- Employers should
ensure that each time a crane is set up, it is level and the outrigger
floats are supported by firm stable footing.
- Employers should
ensure that equipment manufacturer's recommended safe operating procedures
for crane setup and lift configurations are followed.
- Employers should ensure that all crane components are properly rigged while lifting operations are being conducted.
Case
#13: Construction Laborer Crushed by Asphalt Truck While
Paving Interstate Highway |
A 34-year-old construction laborer was fatally injured when he was crushed beneath an asphalt-carrying tractor trailer while paving a six-lane interstate highway. The 11-person crew was paving the northbound side of the highway. The high-speed lane and the middle lane had been closed to traffic. Tractor trailers delivering asphalt paving material were queued on the shoulder and partially in the high-speed lane. Two pavers were operating simultaneously in staggered positions in adjacent lanes. Paver #1 was in the far left (high-speed) lane. Paver #2 was in the middle lane staggered some distance behind paver #1, allowing trucks leaving paver #1 to pull into the middle lane to leave. Usually, trucks waited to be signaled to approach the paver, but sometimes drivers backed up as soon as they saw the previous truck leave the paver.
At the time of the incident, the driver of the truck next in line for paver #1 had just reentered the cab of his truck. About a minute later, the victim went over to shovel old asphalt from around the catch basin located approximately 12 feet behind the waiting tractor trailer filled with asphalt. The driver saw a truck pull away from paver #1 into the adjacent middle lane, started backing up, and then heard people yelling and the truck driver working at paver #2 blowing his air horn. He stopped and found that the four left rear wheels had completely passed over the victim. The county medical examiner pronounced the victim dead at the scene. The cause of death was crushing injuries of the head and torso.
To prevent similar fatalities, investigators recommended the following measures:
- Construction
employers should ensure that one person be designated as a spotter to
direct trucks backing up within highway construction sites.
- Trucking company
employers should design, develop and implement a comprehensive safety
program that includes, but is not limited to, training for truck drivers
in hazard recognition on construction sites and providing back-up alarms
on trucks.
- Highway paving
contractors should design, develop and implement a comprehensive safety
program that includes, but is not limited to, training for highway workers
in controlling traffic hazards on highway construction sites.
- Tractor-trailer manufacturers should consider providing back-up alarms and back-up lights as standard equipment on new vehicles.
Case
#14: Crane Operator Falls 30 Feet from a Crane While Working from
a Freeway Overpass
|
A 60-year-old equipment operator died after falling 30 feet from the crane he was operating on an elevated freeway. The freeway was approximately 25 feet wide from concrete guardrail to concrete guardrail. The crane was being used to set 12-inch x 12-inch timber stringers on top of the falsework on the west side of the elevated freeway. Witnesses stated that he had pulled in the outriggers on the east side to let a truck go by and had not extended them afterward. Coworkers stated that it was common practice for the crane operator to pull in the outriggers in order to allow trucks to go by. The victim continued to lift three more timbers and place them on the falsework. He then climbed down from the crane for a brief discussion with the foreman. Returning to the crane, he began to rotate the boom to the east side and over the rear of the crane. The boom was rotated at approximately an 80 degree angle from the horizontal position and was extended approximately 60 feet. Coworkers stated that they heard the crane making creaking sounds at the time. One witness stated that the victim came out of the cab and shouted "get out of the way." The crane fell over quickly and the victim was thrown to the east side, struck the boom several times, then fell approximately 30 feet to the ground. The end of the boom landed on the freeway without incident. The victim was not wearing a seat belt or hard hat. When city fire paramedics arrived 20 minutes later, they found the victim without a pulse or spontaneous respiration. The coroner listed the cause of death as craniocerebral trauma.
To prevent similar fatalities, investigators recommended the following measures:
- Employers should
ensure that operators extend and set crane outriggers when the load
handled exceeds the rated load without the outriggers.
- Employers should
require that there be a qualified signal person or oiler working with
the crane operator to provide assistance to the operator.
- Employers should
establish, as part of their site planning, a specification which does
not require crane operators to retract outriggers for any type of vehicular
traffic.
- Employers should
require that crane operators wear seat belts at all times during operation.
- In addition, manufacturers and product designers should consider designing cranes with control systems that prohibit or limit certain maneuvers for specific load, boom, and outrigger configurations.
Case
#15: Construction Laborer Dies After Being Run Over by Asphalt Roller
at Highway Construction Site
|
A 37-year-old construction laborer died after being run over by an asphalt roller during a highway paving operation. A seven-person crew was engaged in paving the westbound lanes of a four-lane U.S. highway. At the time of the incident, the crew was paving the right lane and traffic was moving in the left lane. The victim was assigned to walk back and forth along the highway, checking the traffic cones positioned along the dotted lines at the center of the highway to ensure they were standing upright, and ensuring that the construction-zone warning signs remained standing. As the foreman of the crew operated the paving machine, the asphalt roller followed behind to smooth the newly laid asphalt. The roller operator was transporting another employee, who was standing at the front of the machine, leaning against the roll bar and looking backward. The operator made a forward pass with the roller, stopped the machine, then put it in reverse gear. The machine had traveled approximately 10 feet when the operator sensed that something was wrong; at the same time, the rider alerted the operator to stop the roller. The victim was discovered lying face down with his arms at his sides, his head crushed by the roller. The foreman radioed emergency personnel. A local fire department responded within 15 minutes, followed by a rescue squad and the state police. The victim was pronounced dead at the scene. The autopsy report indicated that the cause of death was a crushed skull.
A passing motorist who witnessed a portion of the incident told state police she saw the victim's right shoe get caught by the left side of the metal plate that ran across the back of the machine. She stated that he was on his back, then raised himself to a sitting position. She last observed him pushing against the metal plate.
To prevent similar fatalities, investigators recommended the following measures:
- Employers should
ensure that equipment operators are trained to check work areas for
the presence of pedestrians in the machine's path before changing the
direction of travel.
- Employers should
ensure that passengers are not permitted to ride on rollers or similar
mobile equipment.
- Manufacturers should consider equipping machines that must change direction frequently (such as rollers) with sensors to detect the presence of persons in the machine's path.
Case
#16: Construction Worker Dies After 9-Wheel Pneumatic
Roller Rolls Over on Her |
A 39-year-old construction worker died of injuries sustained when the 20,000-pound 9-wheel pneumatic roller she was driving rolled over on her. She had worked for the employer for 3 months (2 days at the incident site) and had previous operating experience. The roller's drive system consisted of a four-speed manual transmission coupled with a variable-speed hydrostatic drive. This configuration required the operator to manually place the transmission in one of four gears while the roller was stationary. The drive system enabled the operator to change the direction of travel without shifting the manual transmission between gears. The normal operating speed of the roller was 3 to 5 mph. When the roller was being driven from job to job, speeds of up to 15 mph were possible. The roller was not equipped with a rollover protective structure.
Prior to the incident, the victim was operating the roller near the top of a one-half mile hill. After compacting the asphalt near the crest of the hill, she drove the roller downhill around a curve in the road. She may have shifted the roller into neutral while attempting to shift into a lower gear. However, once the machine was in neutral, it was not possible to shift into a lower gear, and the roller began to accelerate down the hill. As the roller continued downhill, the victim was able to steer it around a paver and three other paving company employees. She then left the paved road and drove on the gravel portion of the road for another quarter of a mile. The roller, traveling between 40 and 50 mph, entered a ditch and traveled approximately 100 feet before striking a rock embankment. The roller traveled across the rock embankment another 41 feet before it rolled upside down. The victim was pronounced dead at the scene. The cause of death listed on the death certificate was severe head trauma.
To prevent similar fatalities, investigators recommended the following measures:
- Pneumatic rollers
should be equipped with a rollover protective structure and a seat belt;
older pneumatic rollers should be retrofitted with a properly designed,
manufactured, and installed rollover protective structure and seat belt.
- Employers should design, develop, and implement a comprehensive safety program.
Case
#17: County Highway Department Worker Crushed
When Dump Trailer and Truck Tipped Over |
A 47-year-old county highway department worker was crushed when the dump trailer and truck he was directing tipped over onto him. The victim was part of a five-person crew installing a culvert drain across a county road. He began guiding a truck driver to the edge of the culvert. As the driver started to raise the dump bed, the victim was standing on the right side toward the rear of the trailer. As the trailer began to dump the load of fill around the culvert drain pipe, the fill dirt on the right side remained in the bed while the fill on the left side began sliding out. The uneven weight distribution caused the trailer to tip. The victim began running parallel with the trailer as it was beginning to tip. As the trailer tipped, it brought the truck along with it. The victim reached the area around the passenger side door of the truck when the truck tipped over onto him. Emergency personnel were called to the scene. Extrication was initiated by cutting off the top of the cab and lifting the truck with a track hoe. The victim was conscious during the extrication process. When the weight of the truck was released, the victim began hemorrhaging internally and died at the scene. The cause of death listed on the death certificate was traumatic shock and massive hemorrhaging. The truck driver sustained minor injuries.
To prevent similar fatalities, investigators recommended the following measures:
- Employers should
establish and enforce standard procedures to immediately alert the operator
when loaded material in a dump trailer or truck becomes lodged within
the dump bed during dumping operations. All employees on site should
be trained to follow these procedures, and to identify hazards associated
with instability of loaded materials.
- Employers should
develop, implement, and enforce a comprehensive safety and health plan
that addresses the hazards associated with heavy equipment and takes
into consideration the manufacturer's safety recommendations for operation
of the equipment.
- Employees working
with heavy equipment operators may use signaling devices such as a whistle
or radio contact in order to alert the operator when a problem arises.
This allows the employee to notify the operator immediately from a safe
distance.
- Employees should be trained to maintain safe working distances and work within the line of sight of the operator.
Case
#18: Asphalt Machine Runs Over and Kills Worker
|
A 35-year-old road construction worker died after being run over by a 40-ton asphalt road-widening machine. The victim, who had been on the job only 4 days, was part of a nine-person crew that was widening a state highway in preparation for resurfacing. The victim (the ground man) and the machine operator were working alone, laying down a strip of asphalt on the right shoulder of the road. The crew normally laid two layers of asphalt: the machine moved slowly forward applying the first layer, then backed up to lay the second layer. The victim's job was to walk to the side and rear of the road widener, adjusting the width and height of the asphalt strip according to changing road conditions by adjusting the machine's side-mounted spreader arm.
The machine operator was seated on the top right side of the machine and had just finished applying the first layer of asphalt. He yelled to the victim, who was to the right and rear of the machine at a safe distance. The operator then began to back up the machine, avoiding cones and other barriers on the road. Unknown to the operator, the victim apparently jumped onto the machine as it was backing up, slipped off, and was run over by the right front tire. Although the machine was traveling only a few miles per hour, by the time the operator heard the victim's shouts and stopped the machine, it had already run over the victim. The operator moved the machine off the victim and rushed to his aid. The victim's left leg was amputated below the knee. He was transported to a county hospital, then transferred to a regional hospital, where he suffered multiple complications and died 9 days later. The medical examiner's report listed the cause of death as complications of crush injury to left hemipelvis and left leg.
The victim had frequently been observed walking inside the right arm of the machine, making adjustments using an auxiliary control panel mounted on the side of the machine. Normally these adjustments were made by the machine operator, taking verbal directions from the ground man. It is possible the victim was attempting to make some adjustments while the machine was backing up. At the time of the incident, the machine had an operating backup alarm. Crew members reported that the victim appeared fatigued that day and was perhaps not fit for duty.
To prevent similar fatalities, investigators recommended the following measures:
- Heavy equipment
operators must always remain aware of the location of workers around
their machines.
- Employers should
enforce policies which prohibit riders on industrial equipment or vehicles
that are not designed for passengers.
- Workers who are
not fit for duty due to illness or fatigue should not be assigned to
hazardous tasks.
- To eliminate injury risk from walking inside the wing trying to make adjustments while the machine is in operation, modify the side-mounted auxiliary control panel with a remote control which can be safely actuated by the ground man walking at a safe distance behind the machine.
Case
#19: Highway Department Supervisor Struck by Reversing Dump Truck
|
A 55-year-old highway department supervisor died from injuries sustained after being struck by a reversing dump truck at a multi-lane highway repair project. He had been employed by the company for 30 years, and had worked at the incident site for the previous 2 weeks. The incident occurred on a heavily traveled metropolitan six-lane highway with a center divider. Counting the highway entrance acceleration lane, the incident area was four lanes wide. The crew was to patch potholes and lay down a new layer of asphalt. On the day of the incident, they had set cones and closed down all three travel lanes and the acceleration lane to traffic.
The driver of the dump truck involved in the incident was directed to the start of the patch area. The spotter then set the chains on the dump gate. The driver was then instructed to raise his bed and begin spreading the load of asphalt. At the end of the patch, the driver was instructed to lower the bed and stop the mix. He then pulled forward a short distance and parked next to the oil distributor truck. The victim, in his role as the job-site superintendent, instructed the spotter, the dump truck driver, and the distributor truck driver to lay down another patch beside the first one. He turned and walked along the shoulder. The dump truck driver and the distributor truck driver decided that the dump truck, then the oil distributor truck, would back up to the starting point of the patch. The dump truck then pulled into the rightmost traffic lane and started backing. At some point the supervisor crossed from the shoulder into the lane used by the reversing truck. The truck driver did not see the victim and backed over him. Witnesses tried to warn the victim and the driver, rushing to the site to halt the truck. Local emergency medical services (EMS) responded within minutes; however, the victim was pronounced dead at the scene. The autopsy report listed the cause of death as blunt head and chest trauma.
To prevent similar fatalities, investigators recommended the following measures:
- Employers should
ensure that mobile equipment is equipped with well-maintained audible
backup alarms to warn pedestrians of impending equipment movement.
- Employers should
ensure that work procedures minimize or eliminate pedestrians' exposure
to hazards from moving vehicles and mobile equipment, and should enforce
existing policies that establish pedestrian-free zones.
- Employers should consider providing personal audible alarms to pedestrian workers who are exposed to hazards of vehicle movement.
Case
#20: Equipment Operator Dies After Scraper Overturns
|
A 47-year-old male equipment operator died when the scraper he was operating overturned while negotiating a turn. The victim worked for a company that had been contracted to widen a stretch of road as part of a parkway construction project. The crew consisted of two scraper operators, a bulldozer operator, a roller operator, and a site foreman. The crew was removing material from a 40-foot-wide cut area along the east edge of the existing two-lane road and transporting the material to a fill area located along the west edge of the road. The length of haul varied from 200 to 300 yards as work progressed northward. The scrapers normally cut a 6-inch-deep lift, aided by the bulldozer which pushed them through the cut area. Once the scraper was loaded, the bulldozer returned to the mouth of the cut and waited to assist in loading the next scraper. The victim had been moving earth from a cut area to a fill area. Since the lunch break, he had made four or five passes through the cut area. He had been turning in approximately the same area for about 45 minutes. As he was completing a U-turn into the cut area, the right side tire of the scraper's tractor ran up on an elevated berm, causing the machine to slowly tip over to the left. As the machine tipped, the victim apparently abandoned the operator's cab, jumping to the ground where he slipped and fell. As he was attempting to get up and retreat to safety, he was crushed by the top bar of the machine's rollover protective structure (ROPS). A coworker who had been operating a bulldozer behind the scraper immediately notified the job foreman who called for emergency assistance. A local emergency medical service (EMS) responded in 15 minutes; however, because of the extent of the victim's injuries no first aid was rendered, and the victim was pronounced dead at the scene. Autopsy revealed the cause of death to be multiple crush injuries of the thorax, abdomen, and lower extremities.
To prevent similar fatalities, investigators recommended the following measures:
- Employers should
ensure that earthmoving equipment operators are aware of the hazards
of attempting escape from the equipment during overturns and emphasize
that operators remain inside the protection of the ROPS with seat belt
fastened.
- Employers should
ensure that operators of earthmoving equipment are aware of the importance
of maintaining the lowest possible machine center of gravity at all
times.
- Employers should ensure that haul-road routes are free from overturn hazards of sharply contrasting gradients and curves.
Case
#21: Asphalt Roller Operator Dies Following Rollover Incident
|
A 24-year-old asphalt roller operator was fatally injured when a 10-ton asphalt roller rolled over her. The victim was working with a small crew on a highway outer-road resurfacing project. She had a total of 30 hours experience operating the roller on street repairs. This was her first resurfacing project. Her task was to compress the overflow of freshly poured asphalt at an established driveway to create a smooth transition. The street had an upward slope of 5 to 10 degrees and was 23 feet wide. The road curved slightly to the left with no banking. The depth of fresh asphalt on the street was about 3 inches with overflow asphalt on the sides of the road about 10 inches. The entire project covered approximately one-half mile. There was a ditch on the left side of the roller with an approximate 45-degree downward slope from the road surface, with no shoulder present.
At the time of the incident the victim, who was not wearing a seat belt, was driving forward and approaching the edge of the driveway. She did not stop at the edge of the driveway but proceeded toward the road. At this time, only a portion of the front steering roller was on the asphalt road bed. The roller began pushing up a small mound of fresh asphalt instead of rolling over and compressing it. When the back drive roller left the established driveway surface the back end slid toward the ditch. The operator attempted to pull the roller back onto the asphalt by turning the front steering roller to the right and revving the engine. As the unit began to roll over the operator slipped out of her seat, falling in the direction of the rollover and into the path of the rollover protective structure (ROPS). Coworkers were able to pull the victim clear of the roller and called EMS. The cause of death was determined to be traumatic asphyxia.
To prevent similar fatalities, investigators recommended the following measures:
- Employers should
ensure that all employees wear seatbelts during operation of any heavy
equipment equipped with ROPS.
- Employers should
provide workers training on how to react in the event of an equipment
rollover. Employers should implement a training program specifically
tailored to operators and their assigned equipment.
- Employers should provide worker training for hazard recognition and avoidance, along with safe work practices.
Case
#22: Construction Laborer Dies After Being Struck by a Front End
Loader at a Construction Site
|
A 20-year-old construction worker was struck by a front end loader at a construction site and died 13 hours later. The incident occurred at a concrete batch plant operated by a private contractor which accepted shipments by truck of sand and stone used to produce concrete. The facility included separate sand and stone bays, and a hopper to mix the raw materials and transport them via conveyor belt to a large mixing tank where concrete was produced. The concrete was then transported by truck to an interstate highway construction site nearby.
The area of the facility used for incoming shipments consisted of a 100-foot by 110-foot sand bay and a 130-foot by 130-foot stone bay, separated by a 25-foot-wide mixing hopper. The maneuvering area in front of the hopper and raw material bays was approximately 240 feet wide by 130 feet deep. A front end loader was used to move the raw material from the bays to the mixing hopper. A 40-foot-wide by 48-foot-deep earthen ramp was constructed in front of the hopper for use by the front end loader. The remaining area in which incoming trucks could maneuver was approximately 240 feet wide by 60 feet deep.
The victim had worked on site for approximately 15 days. On the day of the incident, he started work at approximately 7:00 a.m. and was assigned to collect shipping manifests at the entrance to the facility and direct incoming trucks to dump their loads in the sand and stone bays. He had performed these duties for 8 of the 15 days he had been at the site. He was wearing an orange reflective safety vest. At approximately 11:30 a.m., the victim directed a truck into the sand bay located to the left of the mixing hopper. The truck was dumping its load of sand when the victim walked behind the toe (bottom) of the earthen ramp located in front of the mixing hopper. A front end loader backing down the earthen ramp struck the victim approximately 24 feet from the toe of the ramp with the left rear tire, backing over him. At the time of the incident, the backup alarm and front horn on the front end loader were not operational. A state Department of Transportation official who witnessed the incident alerted the loader operator to stop. Emergency personnel arrived within minutes and administered first aid. The victim died 13 hours later at an area hospital. The autopsy report listed the cause of death as multiple blunt force trauma.
To prevent similar fatalities, investigators recommended the following measures:
- Employers should
ensure that backup alarms, horns, and other safety equipment on construction
machinery are functional and tested daily. Equipment that has nonfunctioning
backup alarms, horns, or other safety equipment should be removed from
service until it is repaired.
- Employers should ensure that construction workers who are directing traffic flow are placed in a location where they are visible to equipment and vehicle operators. The site layout should be designed for efficient and orderly traffic flow and with personnel safety in mind. Site-specific traffic control procedures should be designed and implemented to allow for construction-site traffic and safe personnel mobility.
Case
#23: Worker Dies After Being Run Over by a Front End Loader
|
A 31-year-old worker died of injuries he sustained after being run over by a front end loader at a construction site. On the day of the incident, the crew was working at a site where asphalt and concrete were pulverized by a crusher into material to be used for new road bases. One of the workers was operating a large front end loader equipped with a bucket to transport the asphalt and concrete to the crusher. His task was to pick up uncrushed material, drive up an earthen ramp, and dump it into the crusher. He then backed down the ramp and went to pick up additional material.
Shortly before the incident, the loader operator dumped material into the crusher and backed down the earthen ramp. After reaching the bottom of the ramp he turned the loader and continued to back across the work site. Although he knew that the victim was in the general work area, he was not aware the victim was walking in the immediate vicinity of the loader. As the operator turned the loader and continued to back across the work site, he felt the right front wheel of the loader strike something. He continued to back a short distance and then observed the victim lying on the ground in front of the loader. A coworker contacted emergency personnel, who arrived shortly thereafter and pronounced the victim dead at the scene. The cause of death listed on the death certificate was multiple blunt force injuries. The loader was equipped with an enclosed cab. The distance from the roof of the cab to the ground was 13 feet, 7 inches. The operator's view was obstructed only in the areas directly beyond the cab's corner support columns. However, the size of the loader made it difficult for the operator to see workers or objects in close proximity to the loader. The loader was equipped with an audible back-up alarm, but it was not working at the time of the incident. The loader had three reverse gears that allowed speeds from 4.9 mph to 14.6 mph.
To prevent similar fatalities, investigators recommended the following measures:
- Mobile equipment
should be equipped with an audible back-up alarm as well as sensing
units to detect pedestrian workers in the blind spots of equipment operators.
- Employers should
ensure that equipment is always maintained in the proper working condition.
Employers should ensure that heavy equipment is driven in a forward
direction as much as possible.
- Employers should design, develop, and implement a comprehensive safety program.
Case
#24: Laborer Run Over by Dump Truck While Paving Parking Lot
|
A 19-year-old laborer (victim) died after being run over by a dump truck filled with asphalt. The victim worked for a paving company that was contracted to pave the parking lot of a small office complex. At the time of the incident, the victim was leveling and smoothing freshly laid asphalt with a lute. He was in the "danger zone" area between the dump truck and the paver, smoothing a section of asphalt near the edge of a previously laid strip of asphalt. He had received training that specifically addressed the hazards associated with the fatality and he had been warned twice about not entering the area between the front of the paver and a loaded dump truck backing toward the paver. The dump truck driver did not see the victim as he backed toward the paver with a load of asphalt. Although the truck's back-up alarm was sounding, the victim did not move as the truck approached. The truck driver noticed a nearby skid-steer loader operator and the paver operator signaling him to stop. He stopped the truck and then drove forward over the victim again with the truck's rear passenger-side dual wheels. Coworkers immediately placed a call to emergency medical personnel who arrived at the scene shortly after being called. The victim was transported to a local hospital where he was pronounced dead.
To prevent similar fatalities, investigators recommended the following measures:
- Employers should
designate a single on-site worker who has responsibility for authorizing
and directing the movement of certain vehicles, such as trucks traveling
in reverse.
- Mobile equipment
should be equipped with sensing units to detect pedestrian workers in
the blind spots of the equipment operator.
- Employers should design, develop, and implement a comprehensive safety program.
Case
#25: Electrician Dies After Falling From Cherry Picker Basket
|
A 41-year-old male electrician (victim) died after he fell from the basket of an aerial lift truck. The victim and two coworkers were installing electrical wiring for a changeable message sign on the side of a highway bridge. The two leftmost traffic lanes were closed to traffic. The workers arrived at the scene with a pickup truck and a truck equipped with a basket-type work platform attached to a hydraulic boom. After arriving at the site the victim entered the basket, swung it beneath the bridge and raised it up between two of the bridge beams. The victim determined the length of steel pipe needed for the electrical wires and verbally told his coworkers the required length of pipe. At this time the basket was positioned above the closed traffic lanes. While the coworkers cut the pipe, the victim apparently moved the basket to a location above the nearest open traffic lane.
A semi-truck approached the site and observed warning cones and signs directing traffic to merge to the right. The driver proceeded toward the work site in the open traffic lane nearest the closed lanes at approximately 60 mph. When the truck was about 50 feet from the workers' vehicles, the truck driver noticed the basket over the traffic lane in which he was driving. Before the driver could slow the truck or safely move to the next lane, the semi-truck struck the cherry picker basket. The collision caused the victim to be thrown from the basket to the surface of the roadway. Coworkers who heard the collision and saw the victim fall used a cell phone to place a call to emergency personnel. Emergency personnel arrived shortly after being notified and pronounced the victim dead at the scene.
To prevent similar fatalities, investigators recommended the following measure:
- All workers and equipment should remain or be kept within the boundaries of established work zones.
Case
# 26: Heavy Equipment Operator Pinned After
Bulldozer Slides off Flatbed Trailer |
A 45-year-old supervisor for an excavation construction company died when the bulldozer he was driving onto a flatbed trailer overturned, pinning him underneath. The victim had returned to a residential construction site accompanied by his wife, to load the bulldozer and transport it back to the company shop. He parked the truck and trailer across the two-lane road from the driveway of the residence, with the left wheels on the road and the right wheels on the shoulder. There was a slight downhill grade on the shoulder to the ditch. Light rain was falling at the time of the incident, and the trailer was wet. The trailer was equipped with two metal and wood ramps that led from the ground to a wooden "beavertail" platform. After one unsuccessful attempt to drive the bulldozer onto the platform, the victim drove up the ramps and partway onto the platform. The tracks of the machine began to slide sideways towards the ditch, and off the trailer. He tried to jump out of the cab, but was pinned beneath the cab structure when it landed on top of him. The victim's wife, who had witnessed the incident from the passenger seat of the truck cab, flagged down a passing car to call for help. EMS responders elevated the bulldozer with air bags and blocks to remove the victim's body. They noted the unfastened seatbelt dangling from the seat. The victim was pronounced dead at the scene by the medical examiner. The cause of death was crushing chest injuries.
To prevent similar fatalities, investigators recommended the following measures:
- Workers should
always use an operator restraint system while operating equipment equipped
with rollover protective structures (ROPS).
- Employers should
implement work procedures requiring that work crews (including bulldozer
operators) evaluate the terrain prior to loading track equipment onto
a trailer, and plan safe strategies for addressing the hazards.
- Employers should designate a qualified observer to provide verbal or signal directions when track equipment is being loaded onto a trailer.
Case
#27: Member of Road Crew Struck by Semi
|
A 56-year-old senior highway maintenance worker was killed when the vehicle he was operating was struck from the rear by a semi on an interstate highway. The victim was driving the trail vehicle of a three-vehicle highway striping crew. On the day of the incident the victim started his shift at 7:00 a.m. He worked in the maintenance yard in the morning. The incident happened in the afternoon at approximately 3:30 p.m., only 6 or 7 minutes after the striping operation had begun.
The striping operation consisted of three vehicles. The lead vehicle was the striping machine and it was followed by a trailing vehicle with beacons and a "WET PAINT" sign. The incident vehicle was in the rear and was equipped with beacons, a "WET PAINT" sign and a roof-mounted flashing arrow board with the arrow flashing to the right. Separation distance between each of the vehicles was approximately ¼ mile to allow for the paint to dry. All three vehicles were in the left lane of the eastbound lanes of the interstate.
All three vehicles in the striping operation were moving east at approximately 18 miles per hour. A semi and trailer was passing two other semis going east. Weather conditions were optimal and the semi driver had a clear, unobstructed view of the road for approximately 15 seconds prior to the crash. The driver of the front semi that was passed also stated the driver of the incident semi appeared to have sufficient room to pull back into the right lane before impact. From the skid marks at the incident site it appears the driver of the incident semi applied the brakes approximately 1.7 seconds prior to impact. His estimated speed prior to applying the brakes was 75 to 80 mph. He struck the rear vehicle, which was a 1989 Chevrolet Suburban, and it flipped over one time and came to rest upright in the median, 195 feet from the point of impact. The driver of the vehicle that was struck was not wearing a seat belt. The impact caused him to slide up and back and he struck his head, and broke his neck. He was killed instantly.
To prevent similar fatalities, investigators recommended the following measures:
- Employers should
ensure that for mobile striping operations on a multilane road, the
rear vehicle is equipped with a truck-mounted attenuator (TMA) and that
it travels on the shoulder if possible.
- Employers should
ensure that vehicle operators and occupants always use vehicle restraint
systems.
- Employers should
consider using a combination of white, orange, or blue strobe lights
mounted on all vehicles in the striping operation.
- Consideration
should be given to using a more durable method of striping than painting,
such as heat inlaid tape, thermoplastic striping, or tape laid in grooves
in the pavement, that would decrease worker exposure to hazards.
- Training for mobile operations should address the need to constantly scan rearview mirrors for quickly approaching traffic as well as procedures to avoid collision.
Case
#28: Female Construction Worker Dies in a Compactor Tip
Over at a Highway Construction Site |
A 38-year-old female equipment operator (the victim) died when she was partially thrown from the compactor she was operating when it tipped over an embankment and pinned her beneath the ROPS. The employer had been subcontracted to construct a highway off ramp that would eventually lead to an overpass bridge. The employer had been involved for over 16 months with other construction activities on this particular highway expansion project, but had only been on the exit ramp project for 3 days. On the first day of the exit ramp job, the company had delivered to the site a new compactor equipped with an enclosed cab that incorporated the rollover protective structure (ROPS). Although the new compactor had ROPS, no seatbelts were installed. Unlike the old compactor, with front and rear rollers, which the victim had operated for over a year, the new compactor had a single roller in the front and pneumatic tires in the rear. The victim's job at this site was to compact the dirt ramp in preparation for hard surfacing. The victim was operating the compactor, with the enclosed cab door open, back and forth over a built-up road bed. At approximately 1:15 p.m., as she backed the compactor to the road edge, the dirt underneath the rear tire gave way and the compactor tipped over on its side and slid down the embankment. The embankment had an approximate 45-degree slope, and after the compactor slid down the hill on its side it came to rest some 25 feet from the top. When the compactor tipped, the unrestrained victim was partially thrown through the open door, and was pinned underneath the ROPS. Emergency rescue personnel were immediately called and arrived at the site within 15 minutes. The victim was pronounced dead at the site.
To prevent similar fatalities, investigators recommended the following measures:
- Equipment manufacturers,
equipment dealers, and employers should ensure that all ROPS-equipped
vehicles are also equipped with functioning seatbelts.
- Employers should
inspect newly delivered equipment to ensure that all safety devices
are available and working properly before accepting equipment and placing
it in operation. Employers should ensure that all operators receive
training on the importance of wearing seatbelts when operating machinery
equipped with ROPS.
- Employees should
comply with company policies that require use of safety devices.
- Employers should comply with state and federal rules and regulations pertaining to occupational safety and health.
Case
#29: Laborer Run Over by Dump Truck at Roadway Resurfacing Operation
|
A 35-year-old male laborer was run over by a dump truck during resurfacing operations on a two-lane municipal road. The eight-person crew began resurfacing where the two-lane and four-lane road intersected. The crew began by placing a new apron of asphalt across the mouth of the intersection. The apron was then rolled while the paving machine proceeded to lay down new asphalt in the northbound lane of the two-lane road. The laborer had been assigned to rake and finish the edge of the pavement where it abutted and joined with the existing concrete curb. As paving operations proceeded northward, he finished the pavement edge up to the back of the paver, which had stopped to await reloading of asphalt mix. The laborer went around the front of the paver and continued walking south in the unpaved lane toward the intersection along the centerline edge of the new mat. At about the same time, a tandem-axle dump truck, leaving the work zone at about 5 mph, was also traveling south in the unpaved lane behind him. As the laborer walked along the center line, the truck passed the paver and the driver glanced in the right-side rearview mirror to make sure that he had cleared the paver. At this time, the laborer was slightly ahead of and adjacent to the truck's right front bumper. The roller operator working behind the paver near the intersection saw him walk in front of the truck. The truck struck and ran over him. The roller operator and the superintendent shouted to the truck driver to stop; however, the driver did not hear the warnings until the truck's right front wheel had passed over the laborer and the lead wheel of the truck's rear tandem axles had started to run over his foot. The driver stopped the truck and reversed it a short distance to free the laborer's foot. Coworkers notified 911, and emergency medical personnel responded within 12 minutes. CPR and first aid procedures were started at the scene and continued while the laborer was transported to a local hospital, about 4 miles from the site. He died at the hospital approximately 1/2 hour after the incident. The medical examiner attributed death to multiple body injuries.
Investigators identified several factors that may have affected the truck driver's ability to see the laborer. The laborer was wearing a white fishing hat which may have been difficult to distinguish from the white hood of the truck. Additionally, the level of the rearview mirrors was significantly higher than the right front edge of the hood, requiring a person behind the wheel to consciously look down to see a pedestrian. Finally, several objects in the front of the truck may have been visually distracting to the driver: the top of the air cleaner (white in color) and the windshield/door post frame; a fan mounted on the dashboard; regulatory stickers affixed to the inside of the windshield directly in line with the corner of the truck hood and the driver; and a red translucent bug shield mounted across the front of the hood.
To prevent similar fatalities, investigators recommended the following measures:
- Employers should
ensure that workers remain clear of moving equipment and that only those
workers necessary to the job at hand be in the area.
- Employers should
consider the use of electronic signaling devices or sensors to warn
equipment operators of the presence of pedestrians in the blind spots
of mobile equipment.
- Employers should
consider providing and requiring pedestrian workers to wear high-visibility
headgear of standardized color.
- Employers, manufacturers, and regulators should carefully evaluate the placement of auxiliary equipment in vehicle cabs.
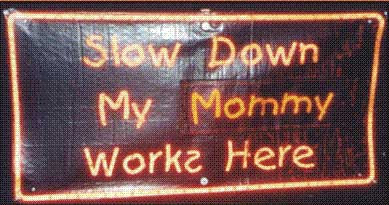
Back to Contents