Summary Statement
One-page summaries of over 100 NIOSH-supported construction safety and health research projects in 2002.
2003
CROSS-CUTTING RESEARCH AND INTERVEN-TIONS IN HAZARDOUS WORK ENVIRONMENTS
RESEARCHERS:Ted Scharf (513) 533-8170
Division of Applied Research and Technology
Bill Wiehagen (412) 386-6468
Pittsburgh Research Laboratory
AFFILIATION: National Institute for Occupational Safety and Health
PURPOSE: Evaluate and implement safety and health interventions that reduce workload or workplace hazards, reorganize the work, and/or provide new information to change how workplace hazards are managed. Enhance the development of cross-cutting research and interventions that focus on the complex relationship among workload, stress, and risks for injury in agriculture, construction, and mining.
RESEARCH SUMMARY: Agriculture, construction, and mining are three of the most hazardous industries in the United States. These three industries consistently rank among the top four for deaths per 100,000 workers. In addition, children and adolescents are at high risk for work-related deaths and injuries in family farming and fishing operations. Standard operating procedures in hazardous industries typically reflect the specific demands and requirements of the tools and hazards that are present in the work environment. But often how these procedures are carried out on the job reflects other, more immediate, demands to maintain productivity.
The work crew performance model (WCPM), developed by the Pittsburgh Research Laboratory, is being implemented in agriculture and construction. Ladder set-up and use has been selected as an application of this model to a small construction setting, while a County Cooperative Extension project dealing with beef cattle farming has been selected to apply the model to agriculture. In the construction component, extension ladder set-up and use checklists have been prepared for evaluation using (1) training at construction sites through a 10-minute toolbox talk, (2) reminders posted on the ladders or on a pocket card about everyday use, and (3) investigations of occupational injuries and fatalities involving extension ladders.
The application of the WCPM has shown that there is a great deal of variability in both set-up and use. The checklists have been designed to address this problem. In FY03, the ladder set-up and use checklists will be evaluated and validated prior to submission for printing as NIOSH numbered documents.
The results from this interdisciplinary effort are expected to lead to (1) interactive tools for workers in the industries under study, (2) improved communication and collaboration among NIOSH scientists and other safety and health professionals working in hazardous industries, and (3) an on-going exploration of cross-cutting approaches to common problems in the three industries.
KEYWORDS: Intervention, work organization, work practices
RECENT CITATIONS:
Lineberry, G.T., T. Scharf, R. Jameson, M. McCann, D. Sulecki, and W. Wiehagen. 2002. An educational intervention for extension ladder set-up and use. In Power Through Partnerships: 12th Annual Construction Safety and Health Conference, Proceedings (May 21-23, 2002, Rosemont, IL).
Scharf, T., C. Vaught, P. Kidd, L. Steiner, K. Kowalski, W. Wiehagen, L. Rethi, and H. Cole. 2001. Toward a typology of dynamic and hazardous work environments. Human and Ecological Risk Assessment, v. 7, no. 7, pp. 1827-1841.
EVALUATING ROADWAY CONSTRUCTION WORK ZONE INTERVENTIONS
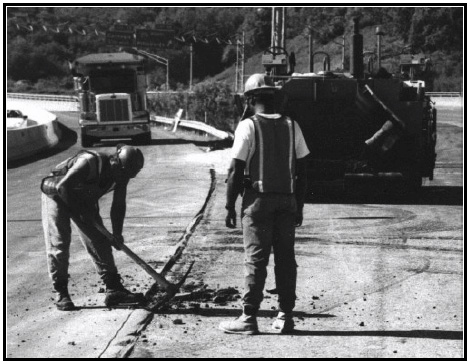
RESEARCHERS:
David Fosbroke (304) 285-6010
Division of Safety Research
Gary Mowrey (412) 386-6594
Pittsburgh Research Laboratory
Todd Ruff (509) 354-8053
Spokane Research Laboratory
AFFILIATION: National Institute for Occupational Safety and Health
PURPOSE: Further field development, evaluation, and demonstration of interventions aimed at reducing worker exposure to equipment and moving vehicles operating inside the boundaries of work zones and other work areas.
RESEARCH SUMMARY: Highway and street construction workers are at risk of fatal and serious nonfatal injuries when working near passing motorists, construction vehicles, and equipment. From 1992-1998, 841 highway and street construction workers were fatally injured. In 465 of these 841 cases (55%), the death was either vehicle- or equipment-related and either clearly or probably occurred in the work zone. In 318 of the 465 vehicle and equipment-related fatalities within work zones, a worker on foot was struck by a vehicle. Victims were as likely to be struck by a construction vehicle as by a passing traffic vehicle.
Road construction is expected to increase by 40% due to increases in federal highway funds under the Transportation Equity Act for the 21st Century. Work zone safety is a priority for labor, industry, and federal and state agency officials who express concern that increases in road construction and structural changes in the industry will lead to increases in worker fatalities. Internal traffic control plans and a variety of proximity warning devices are promising, yet unproven, interventions for preventing fatalities and injuries associated with mobile vehicles and equipment. If proven to be effective, adoption of these interventions could substantially reduce exposure of workers to moving vehicles and equipment, thus reducing fatalities and injuries.
This collaborative project involves the Division of Safety Research, the Pittsburgh Research Laboratory, and the Spokane Research Laboratory. The project consists of four phases: evaluation methods development, intervention development, intervention evaluation and demonstration, and information dissemination and technology transfer. Specific aims include evaluation and design of traffic control plans and methods to reduce worker exposure to moving equipment; assessment of off-the-shelf proximity warning sensors on construction equipment; modification and evaluation of the Hazardous Area Signaling and Ranging Device (HASARD) to prevent collisions between pedestrian workers and construction equipment; and design, development, and assessment of a work zone analysis system for recording and analyzing time and motion studies.
KEYWORDS: Work zone safety, intervention effectiveness, HASARD, proximity warning
RECENT CITATIONS:
Pratt, S.G., D.E. Fosbroke, and S.M. Marsh. 2001. Building safer highway work zones: Measures to prevent worker injuries from vehicles and equipment. DHHS (NIOSH) Pub. 2001-128, 71 pp.
Schiffbauer, W.H. 2001. An active proximity warning system for surface and underground mining applications. Presentation at SME annual meeting, Denver, CO, Feb. 26-28, 2001. Preprint 01-117, 8 pp.
Ruff, T.M. 2002. Evaluating roadway construction work zone interventions—project summary. Presentation at 35th annual meeting of North American Association of Transportation Safety and Health Officials, Overland Park KN, Aug. 12.
EFFECTIVENESS OF ACTIVE SPEED CONTROLS IN HIGHWAY WORK ZONES
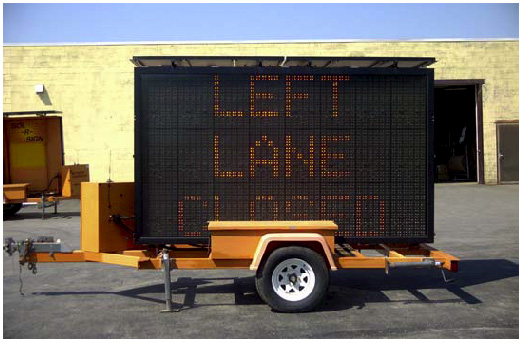
RESEARCHER: Satish Mohan
AFFILIATION: State University of New York at Buffalo (716) 645-2114
PURPOSE: Evaluate the effectiveness of two interventions on the reduction of travel speeds in highway work zones.
RESEARCH SUMMARY: While the injury rate in the U.S. construction industry has declined by 2.9% a year and the fatality rate in the U.S. transportation industry has declined by 3.2% a year, the number of severe injuries and fatalities in highway work zones has stayed constant at approximately 37,000 and 800 a year, respectively, for the last several years, at a cost of $4.0 billion a year. Excessive speed and driver inattention are considered to be the two major causes of highway work zone accidents. The effectiveness of two interventions—rumble strips and variable message signs—are expected to reduce 50% of the injuries and fatalities caused by "excessive speed" and "driver inattention." Rumble strips consist of raised asphalt, pavement grooves, and masking tape. Messages include work zone speed and driver speed. Active speed controls were applied on 65-mph highways in western New York during 1999-2001. All highways had posted speed limits of 45 mph in work zones. Pneumatic road tubes with portable traffic counters were used to monitor speeds. Six types of variable message signs were tested; the effectiveness of each type is given below in order of effectiveness.
- WORK ZONE 45 MPH - PLEASE SLOW DOWN—reduced vehicle speeds by 6 mph.
- WORK ZONE MAXIMUM SPEED 45 MPH - BE PREPARED TO STOP—reduced passenger
car speeds by 4.2 to 5.5 mph and average speeds of all vehicles by 2.9 to 3.7 mph. - WORK ZONE 45 MPH-STATE POLICE ENFORCED—reduced vehicle speeds by 5 mph.
- YOUR SPEED, X MPH-reduced vehicle speeds by 4 mph.
- RIGHT LANE CLOSED-KEEP LEFT and LEFT LANE CLOSED- KEEP RIGHT—were both effective in reducing vehicle speeds by 2.3 mph.
Rumble strips proved effective for the driving lane only, reducing average speeds by 1.2 to 2.2 mph. A different brand of rumble strips combined with POLICE ENFORCEMENT signs reduced vehicle speeds significantly, by 3.0 to 4.5 mph, while standard deviations of the speed of all vehicles decreased by 25% in both in the driving and passing lanes.
KEYWORDS: Work zones, highway safety, highway accidents, intervention effectiveness
RECENT CITATIONS:
Zech, W., and S.B. Mohan. Enhancing work zone safety by implementing speed controls. Washington, DC: National Academy of Sciences, Transportation Research Board. (Submitted)
Ghorpade, B., and S.B. Mohan. Active speed controls for highway work zone safety. Washington, DC: National Academy of Sciences, Transportation Research Board. (Submitted)
ECONOMIC AND JOB HAZARD ANALYSIS OF SANDBLASTING SUBSTITUTES
RESEARCHER: Beth Rosenberg
AFFILIATION: Tufts University (617) 636-6709
PURPOSE: Investigate the range of interventions used to decrease silica exposure in the sandblasting industry and study their health and economic impacts.
RESEARCH SUMMARY: Silicosis is a disabling and often fatal lung disease that is completely preventable. The recent designation of silica as a lung carcinogen by the International Agency for Research on Cancer (IARC) makes the control of silica urgent. The connection between silica and tuberculosis is well known, and, with the rise of drug-resistant tuberculosis, the need to control silica is clear.
Sandblasting results in high silica exposures. NIOSH has produced excellent research on the industrial hygiene aspects of using blasting substitutes, yet there has been little research into the health effects of substitutes not associated with chemical exposures.
With all the much-needed focus on technologies to reduce silica exposure, we must be mindful that we do not introduce new hazards into the workplace. There have been numerous cases of unintended consequences resulting from well-intentioned interventions because the focus has been on controlling a single hazard rather than assessing the full range of impacts in a work environment. To evaluate an intervention fully, we need an integrated approach to the workplace. Furthermore, before any research can be useful in helping contractors decide which method to choose, the economics of each technology must be assessed.
This study will address the potential health and economic impacts associated with substituting other materials for silica sand and the technologies to deliver those substitutes in abrasive blasting.
KEYWORDS: Effectiveness research, sand, silica substitutes, sandblasting
RECENT CITATIONS:
Rosenberg, B.J., E.M. Barbeau, R. Moure-Eraso, and C. Levenstein. 2001. The work environment impact assessment: A methodologic framework for evaluating health-based interventions. American Journal of Industrial Medicine, v. 39, no. 2, pp. 218-226.
Kriebel, D., and B.J. Rosenberg. 200l. Lung cancer: Another good reason to control silicosis. Cancer Causes and Control, v. 12, pp. 785-787.
A STRONG CONSTRUCTION INJURY PREVENTION INTERVENTION AT THE SUBCONTRACTOR LEVEL
RESEARCHERS: Pete Stafford and Buck Cameron
AFFILIATION: CPWR – Center for Construction Research and Training (301) 578-8500
PURPOSE: Lower injuries in construction through the use of methods that can be easily replicated by the entire construction industry. Significantly reduce traumatic injuries related to the great majority of construction accidents by focusing on work planning and specific work practices and controls.
RESEARCH SUMMARY: The proposal aims to show that introducing strong injury prevention methods at the level of the subcontractor can improve safety practices and lower the number of injuries. In the initial phase of the intervention, information will be gathered on industry best practices, which will then form the basis for the intervention safety program. Contractor, foreman, and trade worker responsibilities will be specified. Targeted injuries will include falls, electrocutions, and "struck by" and "caught between pieces of equipment" accident types that account for 90% of construction fatalities.
Forty medium-to-large contractors (that is, contractors with more than 50 full-time- equivalent employees) who do not currently have a strong safety program will be enlisted. These contractors will be drawn from four geographical regions and from a full range of trades represented by the AFL-CIO Building and Construction Trades Department. A like number and type of contractors will be sought as controls.
The intervention will consist of—
- Provision of an OSHA-compliant safety program,
- Provision of supporting training materials,
- Bi-monthly site visits by researchers to audit program compliance,
- Semi-annual progress reports to participating contractors and building trades councils, and
- Collection and analysis of injury data based on OSHA logs and hours worked at the construction sites. While injury data will also be sought from control contractors, experience has shown this to be problematic.
KEYWORD: Intervention, work organization
RECENT CITATIONS:
Stafford, P., and B. Cameron. 2002. Presentation, Southeast Regional Building and Construction Trades Council, New Orleans, LA, Feb. 18, 2002.
Stafford, P., and B. Cameron. 2002. Presentation, Western Regional Building and Construction Trades Council, Las Vegas, NV, March 2002.
Stafford, P., and B. Cameron. 2001. Presentation, Puget Sound Safety Summit, Seattle, WA, Dec. 2001.
CONTACT DERMATITIS PREVENTION
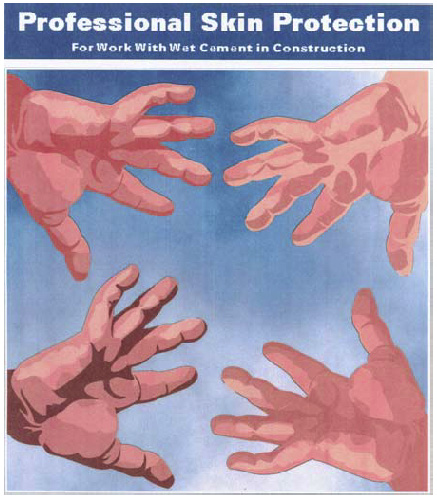
RESEARCHER: Christina Trahan
AFFILIATION: CPWR – Center for Construction Research and Training (301) 578-8500
PURPOSE: Evaluate the effectiveness of job site interventions aimed at the reduction of contact dermatitis among construction workers and the economic impact of occupational contact dermatitis in construction workers.
RESEARCH SUMMARY: As described in the National Occupational Research Agenda, skin diseases are the leading nontrauma-related occupational illnesses in the United States, accounting for 12% to 15% of all occupational illnesses. The exact incidence rate is unclear; estimates range from 67 to 1,700 cases per 100,000. Skin diseases may be recurrent and chronic and result in high direct and indirect costs that may reach up to $1 billion annually. The most common occupational skin diseases are allergic and irritant contact dermatitis, which are preventable diseases. Construction workers are exposed to many harmful substances that can cause contact dermatitis, including portland cement, epoxies, solvents, and preservatives.
Some believe that skin problems affect up to 80% of the workers who have continual contact with products containing portland cement. Found in concrete, mortar, and related construction materials, portland cement is known to cause irritant and allergic contact dermatitis. The alkalinity of wet cement contributes to irritant contact dermatitis, and hexavalent chromium is a strong sensitizing agent responsible for allergic contact dermatitis in cement workers worldwide.
In this project, surveillance activities involve analyses of data from the published literature, occupational exposure surveys, and collection of injury and illness statistics to identify construction workers' exposure to potential dermal hazards. Economic analyses of jobsite and industry-wide interventions are performed, as well as economic characterization of the impact of disease on contractors, workers, workers' compensation systems, private insurance, and society. These interventions are also evaluated as to their effectiveness in reducing contact dermatitis symptoms among the target population.
Materials have been developed aimed at employers, workers, and safety and health professionals regarding the issues and recommended controls relating to contact dermatitis caused by portland cement. A training program has been developed for use by union training centers and employers whose workers come in contact with wet portland cement. Information and publications about contact dermatitis are disseminated to the construction community through a number of CPWR avenues, including employer associations, international unions representing workers in the construction industry, and CPWR's electronic library of construction occupational safety and health (http://www.elcosh.org).
KEYWORDS: Intervention, skin disorders, allergic contact dermatitis, irritant contact dermatitis, portland cement, epoxy, solvents
RECENT CITATIONS:
Professional Skin Protection for Work with Wet Cement in Construction Training Program, PowerPoint presentation with accompanying instructors' guide for 1- and 2-hour training.
Manuals: Employers Guide to Skin Protection for Work with Wet Cement in Construction; Safety and Health Practitioners Guide to Skin Protection for Work with Wet Cement in Construction.
Pamphlets: Save Your Skin-A 15- Minute Tool Box Session; Save Your Skin Glove Wear for Wet Cement Work; Physician's Alert for Occupational Contact Dermatitis Among Construction Workers.
CREW-BASED WORK OBSERVATION PROGRAM TO IMPROVE CONSTRUCTION SAFETY PERFORMANCE
RESEARCHER: Steven Hecker
AFFILIATION: University of Oregon (541) 346-2788
CONSORTIUM: CPWR – Center for Construction Research and Training
PURPOSE: Implementation and evaluation of a modified behavior-based work observation and sampling process to increase construction worker involvement in safety and improve hazard recognition and abatement.
RESEARCH SUMMARY: Construction projects are typically complex undertakings that require extensive coordination among many contractors, trades, and work tasks. Traditional command and control management structures rely on safety policies and procedures developed by the construction manager or general contractor. The transient nature of construction sites means that environmental conditions change rapidly and worker turnover is high. Efforts to involve workers in the safety process may take place through toolbox meetings, safety committees, or suggestion systems, but the high turnover of workers on a construction site inhibits continuity of participation.
This study introduced and evaluated a crew-based work observation process at a large construction site in the Pacific Northwest. The process, Best Practices Sampling (BPS), draws on work sampling and observation elements from behavior-based safety programs implemented in fixed industry. The distinguishing feature of BPS is that the crew is responsible for designating the critical safety items it will monitor and defining best-practice criteria.
Crews from four trade contractors representing four different crafts and working under a single general contractor on the same project participated in the study. Following a 2-hour training session during which crew members were introduced to performance management and self-management concepts, the crew or work team, in a facilitated process, developed a list of best practices required for safe performance of their work tasks. Each crew member was instructed to take 5 to 10 minutes at random every day to observe the work area, tools and equipment, work methods, and worker behavior. The observer noted each time an item was observed and marked it either "best practice" or "needs improvement." All crew members were expected to participate in the development of this list and in defining the best practice for each item based on their knowledge and experience in the trade. Sampling cards also provided space for written comments on any safety matter observed.
The initial findings suggest that worker-based safety processes hold great potential but are extremely fragile. Crews that perceived the highest levels of organizational support for the intervention provided the highest number and highest quality comments concerning existing safety procedures and conditions. Likewise, perceived supervisor and foreman support for the BPS process was also associated with higher levels of BPS activity among crew members.
Results were largely consistent with the determinants of success for other nonhealth- and safety-related worker involvement programs in other industries, suggesting that general research on worker involvement may be relevant to worker-centered safety interventions.
KEYWORDS: Employee involvement, work observation, hazard identification, behavior-based safety, performance management, best practices
RECENT CITATIONS:
Hecker, S., W. Gibbons, and A. Barsotti. 2000. Best practices sampling: A participatory approach to improve construction safety performance. In Proceedings of the 14th Congress of the International Ergonomics Association (Santa Monica, CA). V. 5, pp. 683-686.
ASSESSMENT OF A SAFETY-IN-DESIGN INTERVENTION ON AN INDUSTRIAL CONSTRUCTION SITE
RESEARCHER: Steven Hecker
AFFILIATION: University of Oregon (541) 346-2788
CONSORTIUM: CPWR – Center for Construction Research and Training
PURPOSE: Evaluate processes and outcomes of a collaborative safety-in-design process implemented by owners, construction managers, and design firms to reduce safety hazards in all life cycles of the facility being constructed.
RESEARCH SUMMARY: Evidence from studies of construction accidents and injuries suggests that a significant proportion of such events originates upstream of the building process, i.e., they are connected to such processes as planning, scheduling, and design. One European analysis attributed up to 60% of construction accidents to decisions or behaviors that took place prior to the construction work itself.
In the course of a number of construction projects, Intel Corp. incorporated elements of a safety-in-design approach. These include "lessons learned" and development of a safety-in-design checklist based on issues identified in the construction and operation phases of earlier buildings. In the design of a prototype semiconductor factory, the company, in collaboration with the project's construction manager and design firm, launched a comprehensive process of safety in design, labeled Life Cycle Safety (LCS), which introduced explicit evaluations of design options in programming and three stages of detailed design. LCS is intended to look at all cycles of the structure: construction, commissioning, operations, maintenance, retrofit, and demolition. A major goal is to involve trade contractors with relevant experience prior to construction when their input can identify potential risks at stages where these risks can be addressed by design changes or, if not, be mitigated in the field. Focus groups were held with journeymen and superintendents from four crafts in the early stages of LCS to develop lists of design considerations having safety, quality, and productivity implications.
To evaluate this process, semi-structured interviews were conducted with a large sample of members of the disciplinary work groups who conducted the LCS reviews during programming. Interviews and focus groups have been held with the LCS team that directed the process, representatives of the three organizations who facilitated LCS evaluations in the design phase, and the designers of the project. The comments generated by the LCS evaluations are being coded for analysis. Craft foremen from all disciplines are being debriefed as their scope of work ends to collect data to compare to the design items identified in prior focus groups. Injury data from the construction phase will be compared to similar data from earlier projects, and incident data from the current construction project will be analyzed to link incidents and injuries to design issues either identified in the LCS process but not modified or missed by the process.
KEYWORDS: Safety, design, construction, life cycle
RECENT CITATIONS:
Hecker, S., B. Gibbons, and A. Barsotti. 2001. Making ergonomic changes in construction: Worksite training and task interventions. In Applied Ergonomics, D. Alexander and R. Rabourn, eds. London: Taylor & Francis, pp. 162-189.
ZERO-ACCIDENT WORKSITES: THE ROLE OF OWNERS IN CONSTRUCTION SAFETY
RESEARCHER: Jimmie Hinze
AFFILIATION: University of Florida (352) 392-4697
CONSORTIUM: Construction Safety Alliance
PURPOSE: Examine owner practices as they pertain to construction safety. Evaluate the effectiveness of owner involvement in construction safety through contractor selection, contractual requirements, and active participation during the construction process.
RESEARCH SUMMARY: Owners of facilities being constructed play a pivotal role in construction safety. This role begins with selecting a contractor(s) and the contractual requirements imposed on the contractor. It continues during the construction phase through the active involvement of the owner in construction safety.
Information on the nature of owner involvement in construction safety was obtained through personal interviews with owner representatives for over 70 large construction projects. This phase, data collection, is nearing completion.
The next phase of the research will be to compile various owner practices employed to promote construction safety. This will reveal the nature of the variability that exists in owner practices on different projects. The data will then be examined to identify those practices associated with better injury rates as defined as the number of OSHA-recordable injuries incurred per 200,000 hours of worker exposure.
The data analysis will be conducted in the fall of 2002, and the research report will be completed by the end of spring 2003.
KEYWORDS: Facility owners, contractor selection, contract requirements, monitoring safety, safe procedures
A BLUEPRINT FOR INTEGRATING HEALTH HAZARD CONTROL PROGRAMS INTO INFRASTRUCTURE REHABILITATION
RESEARCHERS:
Mark Goldberg (212) 481-7555 Hunter College, City University of New York
Stephen Levine (212) 241-7811
Nancy Clark (212) 241-0108
Mt. Sinai School of Medicine
CONSORTIUM: CPWR – Center for Construction Research and Training
PURPOSE: Develop a guidance system, or blueprint, comprised of best practices that contractors can use to link health hazard controls with the planning and everyday management of construction activities. Assess engineering and work practice controls to reduce lead and silica exposure and enhance the role of labor in implementing control programs.
RESEARCH SUMMARY: Control measures designed to reduce exposures to lead and silica during infrastructure rehabilitation are often difficult to implement or sustain successfully. The blueprint project employs a comprehensive three-pronged approach to improve the integration of health hazard controls into construction projects by (1) developing, implementing, and assessing blueprint guides; (2) assessing the de facto role that labor plays in the implementation of health hazard control programs and enhancing labor's role with a view toward improving health hazard control integration; and (3) assessing lead and silica engineering and work practice controls. In developing and assessing each of these project components, both qualitative and quantitative data collection methods will be employed, including discussion groups with employers and workers; interviews with contractors, supervisors, workers, and union representatives; health hazard control program audits; and industrial hygiene assessments, including biological monitoring where appropriate. This project builds upon a growing body of investigations that suggest that the most effective interventions are those in which workers participate, which stress the importance of management leadership, and which employ multiple exposure control strategies— engineering controls, work practices, and respiratory protection.
The blueprint itself consists of a number of guides that provide practical guidance to project managers, safety personnel, and workers on day-to-day management of health hazard control programs. It is designed to be process oriented, that is, capable of anticipating health hazard control needs within the phases of a construction project, while being flexible enough to protect workers during the constant readjustments typical of construction rehabilitation work.
Each blueprint guide is uniformly structured and provides a brief statement of its purpose followed by sections on planning and scheduling, identification of employer and employee roles and responsibilities, and how to implement and evaluate a "best practice." A resource section contains references, forms, checklists, and lists of readily available information, useful Web sites, and supplies and vendors.
KEYWORDS: Health hazard control management, management control guides, labor participation in hazard control, work site organi-zation, silica control, lead control
RECENT CITATIONS:
Clark, N., and M. Goldberg. 2002. Construction blueprint: Best practices for health hazard controls. Applied Occupational and Environmental Hygiene, v. 17, no. 5, pp. 326-328.
Zuckerman, N., M. Goldberg, and N. Clark. 2002. A blueprint guide for managing silica exposures among workers engaged in concrete and rock, drilling, chipping and crushing. In Power Through Partnerships: 12th Annual Construction Safety and Health Conference, Proceedings (May 21-23, 2002, Rosemont, IL).
Goldberg, M., and N. Clark. 2001. A blueprint for integrating health hazard controls for lead and silica into infrastructure rehabilitation projects. Presentation at American Industrial Hygiene Conference, New Orleans, LA, June 2001.
Clark, N. 2001. Workers' role in lead health and safety programs. Presentation at 11th annual Construction Safety and Health Conference, Rosemont, IL, Feb. 2001.
INTEGRATING SAFETY INTO CONSTRUCTION CPM SCHEDULES
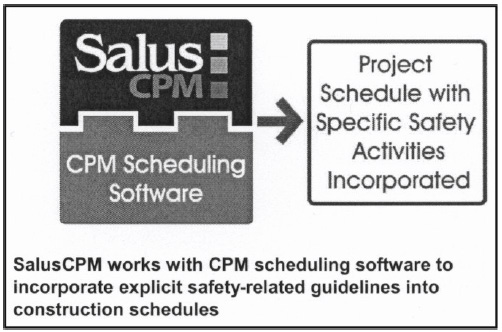
RESEARCHERS:
Jimmie Hinze (352) 372-4697 University of Florida
Jeffrey Nelson (352) 372-9712 Conceptual Arts, Inc.
CONSORTIUM: CPWR – Center for Construction Research and Training
PURPOSE: Develop a software program, SalusCPM, that facilitates the incorporation of explicit safety-related guidelines into construction schedules.
RESEARCH SUMMARY: Critical path method (CPM) scheduling software has become a ubiquitous and indispensable tool in commercial construction project management. Construction schedules are typically developed around work activities that contribute to installing the components to complete a structure or facility. These activities are typically organized sequentially as they occur in the actual construction process and represent a logical progression of work. For most commercial construction projects, it is the schedule, more than concerns for costs or quality, that drives and influences management decisions.
Increasingly, safety has become a major concern on construction projects. However, CPM schedules typically do not address safety issues or concerns, despite a high level of interest in promoting safety. Since most injuries occur during a work activity, it is logical that safety should be emphasized in conjunction with the activities being planned. Some activities have more inherent risks than others. Presumably, if safety concerns were linked with planned activities and explicitly incorporated into schedules, it is more likely that the activities would be performed with a greater focus on safety. If widely practiced, this could ultimately result in a significant reduction in construction-related injuries, illnesses, and deaths.
SalusCPM is a software plug-in that works in tandem with scheduling software, allowing the user to incorporate a project-specific safety plan directly into the schedule. There are four components of SalusCPM: Safety Database, Safety Planner, Safety Integrator, and Safety Manager.
- The Safety Database component currently contains about 2,500 individual safety guidelines prepared by safety specialists and organized into checklists. Each checklist contains a series of guidelines related to a specific type of construction activity.
- The Safety Planner allows the user to select, add, delete, and modify (i.e., customize) the checklist database to suit the safety needs of a particular construction project.
- The Safety Integrator works with the CPM scheduling software and allows the user to insert specific checklists as activities into the CPM schedule. This resulting schedule can serve as the heart of a site-specific safety plan, a regulatory requirement for large construction projects.
- The Safety Manager assists in managing the individual items on the checklist that arise as work progresses according to the schedule.
FALL-SAFE PARTNERSHIP
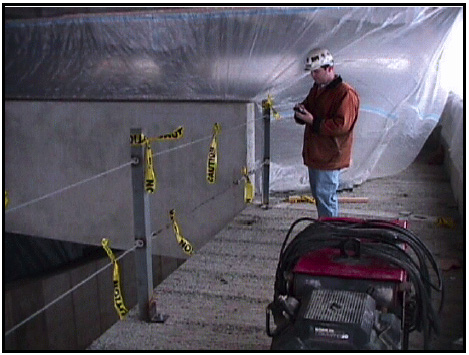
A WVU Fall-Safe coordinator audits a guard rail at a Fall-Safe contractor's site.
RESEARCHER: Paul Becker
AFFILIATION: West Virginia University (304) 293-3096
CONSORTIUM: CPWR – Center for Construction Research and Training
PURPOSE: Determine whether a partnership between third-party safety and health organizations and construction contractors can reduce fall hazards at construction sites through implementation of a fall hazard management program that includes training, safety committees, inspections, accountability, and third-party oversight.
RESEARCH SUMMARY: Falls are the leading cause of fatal-ities and a major cause of injury in construction work. While construction workers represent 5% of the nation's workforce, they account for 49.6% of fall fatalities. In West Virginia, the construction industry accounts for more than a third of all occupational falls, both fatal and nonfatal.
A partnership between West Virginia University (WVU) (and more recently St. Paul Insurance and Construction Safety Council) and construction contractors has been established in which contractors obtain "Fall-Safe" status by implementing a fall hazard management system developed by the university. Important elements of the system are development of company policies, training of supervisors and workers, development of site-specific fall hazard control plans, development of communication and accountability systems on-site to manage fall hazards, and regular site inspections by contractor personnel. Contractors maintain Fall-Safe status by achieving a minimum score on site program and site fall hazard control audits. The audits also act as a service to the contractor by providing feedback to the safety director to further assist in the control of fall hazards on the jobsite.
The research methodology employs a quasi-experimental model that compares outcome measures in an intervention group with measures in a control group. These measures include surveys of employers, supervisors, and employees; audits of construction site fall prevention plans and site fall hazard control efforts; and analyses of fall-related claims to workers' compensation systems. Statistical analysis of the data collected from 16 contractors (10 intervention, 6 control) in a pilot phase of the research indicates that the intervention group of contractors has shown more improvement in site program and site hazard control scores than the control group. Results also indicate that scores for site hazard control audits can be associated with scores on the site program audit.
An unexpected result of the research suggests that a less-intensive intervention such as a user-friendly computerized auditing tool might also lead to changes in contractor safety performance. Given that WVU estimates it will cost approximately $10,000 per year for a contractor to implement the Fall-Safe program (internal costs and fees to the third-party partner), this finding is particularly important.
The study has now been expanded to include 40 additional contractors and the two participating partners of the St. Paul Insurance and Construction Safety Council. The current study tests whether the intervention can succeed when implemented by other third-party organizations in other regions of the country. The higher number of participants will permit the use of workers' compensation injury claims data as an outcome measure.
KEYWORDS: Falls, intervention research, occupational injury
RECENT CITATIONS:
Becker, P., M. Fullen, M. Akladios, and G. Hobbs. 2001. Prevention of construction falls by organizational intervention. Injury Prevention, Supplement, July, pp. 64-67.
Becker, P., M. Fullen, A. Akladios, M. Carr, and W. Lundstrom. 2000. Use of a hand-held computer to audit construction fall prevention effective-ness. International Journal of Computer Integrated Design and Construction, Special Issue on Computerized Safety Management.
QUALITATIVE RESEARCH AND INTERVENTION
RESEARCHER: Susan Moir
AFFILIATION: University of Massachusetts-Lowell (978) 934-3258
CONSORTIUM: CPWR – Center for Construction Research and Training
PURPOSE: Introduce technical and organizational interventions into the construction work environment and evaluate the effective-ness of these interventions in reducing exposures among concrete workers to respiratory hazards and musculoskeletal injuries.
RESEARCH SUMMARY: Partnering with area construction unions and contractors and joint labor-management training programs has resulted in participatory research activities carried out with workers at regional training centers and on construction sites. Three studies were conducted.
- Hardhat Ergonomics was a training program in which popular education methods were used to facilitate classes where workers conducted ergonomic job analyses, identified key agents of change, and role-played strategies for making changes at their workplaces.
- Health Trak was a joint labor/management participatory action research project. Small groups of workers and frontline supervisors met weekly over a 2-month period to identify current hazards on their site and design and propose solutions.
- The Boston-Area Health and Safety for Women in Construction (HASWIC) Research Circle was a standing focus group of tradeswomen who drew on their extensive experience to evaluate working conditions and analyze the roles of workers, unions, contractors, and government in making and impeding changes.
Four contexts that influence intervention effectiveness have been identified: organizational context in which the intervention is being introduced, attributes of the intervention itself, the process by which the intervention is introduced, and approaches to health and safety issues by participating trade unions.
To assess each of these contexts, approximately 50 factors influencing inter-vention effectiveness have been identified, defined, and organized into a matrix describing the specific information sought, source of that information, time (pre- or post-intervention), and method of data collection. This matrix will be used to develop specific protocols for collecting both quantitative and qualitative data for a working model of the effectiveness of intervention studies.
KEYWORDS: Intervention effectiveness, qualitative, highway construction, participatory research
RECENT CITATIONS:
Moir, S., V. Paquet, L. Punnett, and B. Buchholz. (In press.) Making sense of highway construction: A taxonomic framework for ergonomic exposure assessment and intervention. Applied Occupational and Environmental Hygiene.
Moir, S. 2002. Boston's Big Dig: Lessons from efforts to integrate occupational health goals into a large highway development project. Occupational Health and Development, no. 4, pp. 3-11.
Moir, S. 2002. Worker-centered approaches to OSHA training for the future. To be presented at National Conference on Workplace Safety and Health Training.
Back to Contents