Summary Statement
One-page summaries of over 100 NIOSH-supported construction safety and health research projects in 2002.
2003
EVALUATING TOOLBOX TRAINING IN CONSTRUCTION AND MINING
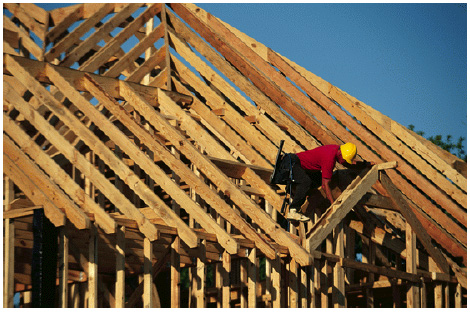
RESEARCHERS:
Herb Linn (304) 285-5900
Division of Safety Research
Carol Stephenson (513) 533-8581
Terri Heidotting (513) 533-8325
Education and Information Division
Lani Boldt (509) 354-8006
Spokane Research Laboratory
AFFILIATION: National Institute for Occupational Safety and Health
PURPOSE: Identify and review existing toolbox/tailgate training materials and programs, prepare new toolbox talks for high-risk construction and mining sectors based on injury and fatality investigation reports, evaluate the effectiveness of these training materials for small construction and mining companies, and use evaluation results to expand toolbox series and distribute them widely to target sectors.
RESEARCH SUMMARY: Construction and mine workers face higher-than- normal risks of fatal injury, nonfatal injury, and illness resulting from on-the- job exposures. During the period from 1980 through 1995, among major industry sectors, construction had the highest number of deaths resulting from workplace injury—over 17,000 deaths, or more than 1,000 deaths per year.
Dun and Bradstreet reports that there are over 213,000 residential building construction companies in the United States. Ninety-six percent of these contractors employ less than 15 workers, and over 80% employ less than five. These small companies do not have the resources to support an on-site safety professional to identify and apply risk and prevention information relevant to their operations or the facilities or resources to provide their workers with formal training programs addressing workplace safety and health.
This research will evaluate the toolbox training approach in the high-risk residential building construction and sand-and-gravel mining sectors. "Toolbox" or "tailgate" training—short (usually 10 to 15 minutes) weekly sessions conducted on-site prior to work shifts and involving work crews—is a primary mode of worker occupational safety and health training employed in small construction companies. Each toolbox talk in the series will contain a narrative "story" of one or more serious or fatal injuries based on available injury and fatality investigative reports from NIOSH, MSHA, OSHA, and other sources. A series of field evaluation studies in sand-and-gravel mining and residential building construction will be conducted to determine whether the NIOSH narrative-based toolbox talks can produce desired results—such as increased knowledge, appropriate changes in attitude, positive changes in behavior and work practices, and sustained changes—when compared to standard, nonnarrative toolbox talks.
This project will fill gaps in current knowledge regarding the effective-ness of short, on-site workplace training sessions for construction work crews, and the critical elements, formats, and approaches of such training sessions that contribute to desired results. A companion project involves developing toolbox training materials for the sand-and-gravel mining sector.
KEYWORDS: Effectiveness research, training
SAFETY CHECKLISTS PROGRAM FOR SMALL BUSINESSES IN THE CONSTRUCTION INDUSTRY
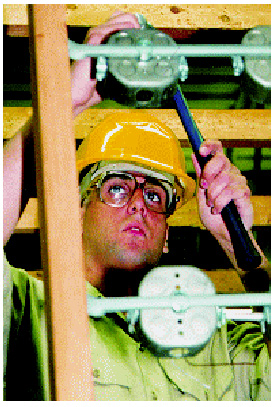
RESEARCHER: John Palassis
AFFILIATION:
Education and Information Division
National Institute for Occupational Safety and Health (513) 533-8136
PURPOSE: Develop and evaluate a prototype document containing checklists of occupational safety and health requirements for small, trade-specific construction businesses.
RESEARCH SUMMARY: The construction industry continues to be one of the most hazardous industries in the United States. Workers of all ages are victims of fatal and nonfatal injuries associated with construction, and each year, approximately 500,000 out of 5.6 million construction workers (which includes many young and new workers) are injured at construction sites. A prototype document containing checklists on safety and health will be developed for specific construction trades and the owners of small construction businesses. The document will include information on how to implement a safety checklist program and how to establish and maintain an effective safety and health and environmental safety program. The document will be designed as an easy self-assessment procedure that will assist business owners, supervisors, and workers in how to recognize workplace hazards and safety and health deficiencies in construction and determine the proper course of regulatory compliance by remediating or controlling hazards. A separate safety checklist for each specific federal occupational safety and health or environmental regulation pertinent to small construction businesses will be included.
The project will build upon a program in vocational safety and health containing 82 safety checklists for administrators and supervisors in vocational education. It will also be made available on CD-ROM with many occupational safety and health databases from other agencies.
The prototype document will be sent to national and international partners for review and evaluation.
KEYWORDS: Safety, small business
RECENT CITATIONS:
Palassis, J., and M. Haring Sweeney. 2001. NIOSH Safety Checklists Program for schools and small businesses. Presentation at Ohio Safety Congress, Columbus OH, April 4, 2001.
Palassis J., and M. Haring Sweeney. 2000. Minimizing injury risk in vocational schools: Safety Checklist Program. Poster paper at American Public Health Association conference, Boston, MA, Nov. 14, 2000.
Palassis J., and M. Haring Sweeney. 2000. NIOSH Safety Checklists Program. Presentation at Alabama Governor's Occupational Safety and Health Conference, Orange Beach, AL, Aug. 29, 2000.
SAFETY CHECKLISTS FOR VOCATIONAL/ TECHNICAL SCHOOLS
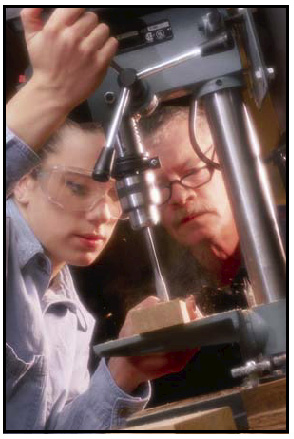
RESEARCHER: John Palassis
AFFILIATION:
Education and Information Division
National Institute for Occupational Safety and Health (513) 533-8136
PURPOSE: Increase awareness of safety and health in young workers.
RESEARCH SUMMARY: In the United States, there are approximately 11 million students enrolled in vocational-technical education programs. Most will graduate to work in a trade shop. The latest estimate from the National Electronic Injury Surveillance System (NEISS) indicate that over 240,000 young workers receive injuries in the workplace each year; of these, 84,000 were treated in hospital emergency rooms in 1999, and in the next year, 73 died from fatal occupational injuries.
Researchers will build upon a vocational safety and health document containing 82 safety checklists developed for NIOSH by the Environmental Occupational Health and Safety Institute in New Jersey. The project proposes to finalize, evaluate, and disseminate a document (in CD-ROM format) to administrators, supervisors, and teachers in vocational-technical schools designed to increase the level of occupational and environmental safety and health within these schools. It will be designed as an easy-to-use self-assessment procedure to recognize workplace hazards and safety deficiencies in vocational-technical school shops. Specifically, it will contain information on how to (1) establish and maintain an effective safety and health and environmental safety program, (2) implement a safety checklist program to identify occupational or environmental hazards, and (3) determine the proper course of regulatory compliance by remediating or controlling the hazard. Safety checklists will address federal occupational safety and health and environmental regulations pertinent to vocational schools.
KEYWORDS: Safety, young workers, hazards, vocational education
RECENT CITATIONS:
Palassis J., and M. Haring Sweeney. 2000. NIOSH Safety Checklists for Vocational-Technical Programs. Presentation at Association for Career and Technical Education Conference, San Diego, CA, Dec. 8, 2000.
Palassis J., and M. Haring Sweeney. 2000. Reducing injury risk of students in vocational-technical schools and young workers in small businesses. Presentation at National Occupational Injury Research Symposium, Special Populations session, Pittsburgh, PA, Oct. 18, 2000.
Palassis, J. 2000. NIOSH Safety Checklists. Presentation at Ohio Safety Congress, Technology and Adult Education session, Columbus, OH, April 6, 2000.
EVALUATION OF ELECTRICAL SAFETY HIGH SCHOOL CURRICULUM
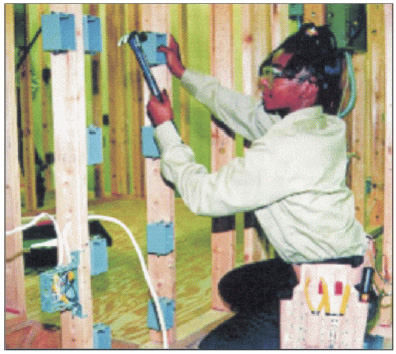
RESEARCHERS:
Thaddeus Fowler (513) 533-8530
Carol Merry Stephenson (513) 533-8581
AFFILIATION:
Education and Information Division
National Institute for Occupational Safety and Health
PURPOSE: Assess the effectiveness of NIOSH-developed occupational safety and health training for young workers in secondary vocational education programs and the benefits of using alternative instructional strategies to increase students' knowledge of and improve attitudes toward occupational safety and health.
RESEARCH SUMMARY: Nearly one-half (48.1%) of all occupational injuries are sustained by employees with less than 1 year of work experience. NIOSH has estimated that over 240,000 adolescents are injured on the job each year; of these, about 84,000 injuries result in emergency room visits in 1999, and 73 young workers died because of work-related injuries.
Little research has been conducted indicating effective strategies for imparting knowledge about safety and health to high school students, nor has there been sufficient evaluation of the effects of a targeted curriculum in changing students' attitudes, beliefs, and behavioral intentions concerning health and safety. Pre-job training in occupational safety and health is one form of intervention that may reduce the disproportionately high rate of injuries occurring in new and young workers. Its effectiveness, however, depends upon how the curriculum is delivered to the students and integrated into their trade programs.
In this project, at least 50 vocational education classrooms will use a newly developed NIOSH curriculum on electrical safety. A critical element that was evaluated was the value added to the curriculum by a motivational/ informational videotape. Students' knowledge gain, safe-work attitudes and beliefs, and behavioral intentions on the job were assessed and compared to students who completed a generic training program in the electrical trades. Assessments were made before instruction began (baseline), post-study, and (as a measure of retention) after summer recess. Both students and teachers had an opportunity to critique the new curriculum.
Study results will be published and disseminated in peer-reviewed literature. Revised curricula have been made available to vocational education programs nationwide, providing guidance for future vocational education programs in other trades. The ultimate goal is to improve the incorporation of safety and health into the 11-million-student vocational-technical system.
KEYWORDS: Evaluation, training, young workers, vocational education
SUPERVISORY TRAINING IN CONSTRUCTION
RESEARCHERS: Jacqueline Villnave and Steven Hecker
AFFILIATION: University of Oregon (503) 725-8424
CONSORTIUM: CPWR – Center for Construction Research and Training
PURPOSE: Identification and implementation of best practices in supervisor training in construction, with an emphasis on the integration of leadership skills training with specific safety and health information.
RESEARCH SUMMARY: In the construction industry, the inherent difficulty of managing employees is complicated by the nature of work organization in the skilled trades. In contrast to other industries, construction foremen are drawn from the ranks of journeymen, and such journeymen may move in and out of supervisory positions, which can lead to role conflict among supervisors.
A variety of factors, including owner and customer demands, increasingly complex technologies, compressed schedules, safety and health concerns, and a more educated work force, are placing increasing demands on construction foremen. The industry has begun to recognize the need for higher levels of leadership and organizational skills, in addition to production skills, for foremen to perform their supervisory tasks effectively. Recognizing the lack of leadership training for foremen as a potentially serious problem, particularly when related to the introduction of worker-based health and safety training, we are assessing the current state of supervisory training and will develop interventions to address current deficiencies.
We identified four Joint Apprenticeship Training Centers (JATC) that offer training for supervisors and three contractors that have internal supervisory training programs. Information about these programs was obtained as a result of direct observation of classroom instruction; interviews with training coordinators, instructors, and participants; and analyses of course material and curricula. We are also gathering data on supervisory training programs developed by national unions and contractor associations. Our initial analysis confirms that safety and health content is limited in these courses, with the emphasis being on production and quality issues, but some are beginning to address leadership and communication skills. Barriers to participation have also been identified, including scheduling, cost, and uncertain rewards for completion.
Based on these data, our research team will develop or adapt a training intervention that combines leadership skills with specific safety and health information. The intention is to create a program that would be viewed as practical by contractors and training centers. Information on specific safety and health risks—for instance, the prevention of sprain and strain injuries— will be incorporated along with skills in communication, motivation, coaching, and dealing with difficult people. We will evaluate the training intervention through questionnaires and interviews with both foremen and the workers they supervise and through an assessment of workplace changes and injury outcomes on projects for which these supervisors are responsible.
KEYWORDS: Supervisor training, foreman training, leadership skills
CONSTRUCTION CHART BOOK
RESEARCHER: Sue Dong
AFFILIATION: CPWR – Center for Construction Research and Training (301) 578-8500
PURPOSE: Characterize the industry for researchers, workers, and others and highlight issues warranting more attention, including the high toll in injuries, illnesses, and deaths in construction.
RESEARCH SUMMARY: An expanded and improved edition has been published. The book has more than 170 charts, 61 of them in the safety and health section, which is comprised of 18 topics.
Since 1995, when the first edition was published, the chart book has been a key reference on the construction industry. The volume, the only source of its kind, provides comprehensive data to characterize the industry. It describes information on sources in federal and state government, private industry, the nonprofit sector, and other countries. Sections include an Industry Summary, Labor Force Characteristics, Employment and Income, Education and Training, and Safety and Health. One new page describes problems with data on safety and health in detail. The book can help anyone interested in construction, from researcher to worker. The format is user friendly, and all pages are posted on the Web at www.cpwr.com and www.elcosh.org.
KEYWORDS: Chart book, data, statistics, industry, safety, health
RECENT CITATIONS:
Dong, S., with R. Chowdhury, M. McCann, C. Trahan, and J. Gittle-man. J. Seegal, editor. 2002. The Construction Chart Book: The U.S. Construction Industry and Its Workers, 3rd ed. Silver Spring, MD: CPWR – Center for Construction Research and Training.
Grob, H., X. Dong, E. Pollack, S. Schneider, and J. Seegal. 1998. The Construction Chart Book: The U.S. Construction Industry and Its Workers, 2nd ed. Washington, DC: CPWR – Center for Construction Research and Training.
Grob, H., X. Dong, E. Pollack, S. Schneider, and J. Seegal. 1997. The Construction Chart Book: The U.S. Construction Industry and Its Workers, 1st ed. Washington, DC: CPWR – Center for Construction Research and Training.
Back to Contents